What is Military Casting?
Military castings are metal parts produced by casting technology. They are used in military equipment, weapon systems and related military facilities. The casting process pours metal materials into a mold of a specific shape. For example, cast steel, cast iron, aluminum alloy, titanium alloy, etc. After cooling and solidification, metal parts with certain shapes, sizes and properties are formed. As a key basic component of the military industry. The quality and performance of military castings directly affect the reliability and safety of military equipment.
JC Casting is a professional military casting foundry and supplier. We are able to provide customers with high-quality, high-performance military castings. Meet strict military standards and customized needs.
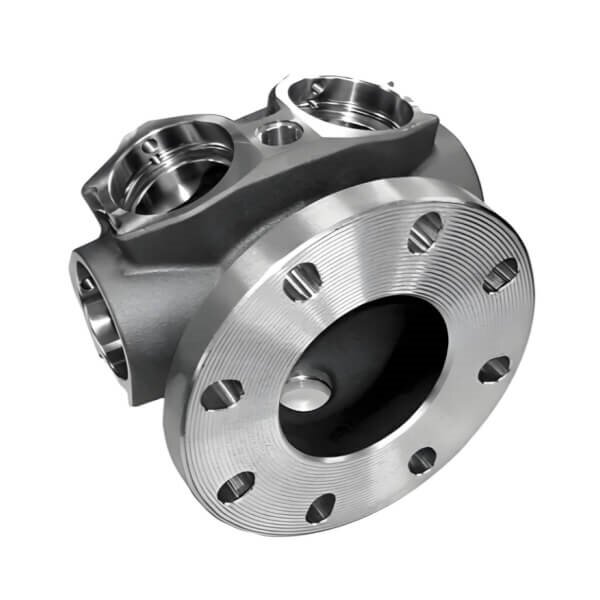
Characteristics of military castings
High performance requirements
Military equipment is often in extreme environments. Such as high temperature, strong corrosion, battlefield impact, etc. So, castings need to have excellent mechanical properties. Such as high strength, high toughness, high temperature resistance, and wear resistance.
High Precision and Complexity
Military equipment has a precise structure. Many castings have complex inner cavities or special-shaped structures. They need to be realized through precision casting. To reduce the amount of subsequent processing. Ensure assembly accuracy.
High reliability and safety
The operating environment of military equipment is directly related to combat effectiveness and personnel safety. So, castings must undergo strict quality inspections. Such as non-destructive testing and mechanical property testing. Ensure that castings are free of defects such as cracks and pores. Avoid risks such as breakage and failure during use.
What are the commonly used military casting materials?
The casting materials of military castings need to be selected according to the use environment of the equipment. Such as high temperature, corrosion, lightweight and other requirements.
Steel materials
- Structural steel: Including carbon structural steel and alloy structural steel. It has high strength and toughness and relatively low cost. It is suitable for structural parts that bear large loads.
- Stainless steel: Contains chromium, nickel and other elements. Strong corrosion resistance. Commonly used in naval equipment and military facilities in humid environments.
Light alloy materials
- Aluminum alloy: Low density. Good casting performance and corrosion resistance. Meets lightweight requirements. Suitable for aerospace equipment and military vehicle housings, etc.
- Magnesium alloy: Lighter than aluminum alloy. Mostly used for weight-sensitive parts. Such as helicopter gearbox housings.
Titanium alloy materials
High strength. Low density. Excellent high temperature resistance and corrosion resistance. It is the core material for aerospace and high-end weapons.
High temperature alloy materials
- Nickel-based high-temperature alloy: Nickel-based alloy with added elements. Such as chromium, cobalt, and tungsten. It can maintain high strength and oxidation resistance at high temperatures. It is the core component of aircraft engines and gas turbines.
- Cobalt-based high-temperature alloys: Better wear resistance and high-temperature corrosion resistance. But the cost is higher. Mostly used for parts that require extreme wear resistance.
Other special materials
- Zinc alloy: Good casting performance. High precision. Often used for small precision parts.
- Copper alloy: Excellent thermal and electrical conductivity. Can be used for heat dissipation components of military electronic equipment, radar waveguide castings, etc.
The selection of these materials depends on the specific military equipment requirements. JC Casting will comprehensively consider performance, cost and process feasibility. To provide customers with the best solutions for military castings.
JC Casting Advantages
- Process technology: JC Casting is a leading investment casting supplier in China. It has its own foundry and CNC workshop. It has rich experience in military casting. It can manufacture military castings of various materials. To meet their specific requirements for materials and processes.
- Product customization: The company has the ability to provide services from single production to OEM and ODM. It can also provide services such as design solutions. Military castings usually need to be customized according to different equipment requirements. JC Casting has comprehensive service capabilities. It can better meet the diverse and personalized needs of the military field.
- Quality control: Emphasize the visibility and controllability of the production process. Have a relatively complete quality control system. Military castings have very high quality requirements. Strict quality control helps ensure that products meet high standards. Reduce defect rates. Ensure the reliability and safety of military equipment.
- Production capacity: We have 2 self-owned factories and 2 cooperative factories. We have a certain production scale. We can handle everything from small samples to large-scale batch production.This allows us to flexibly meet the different order volume requirements for military castings. And also provides corresponding advantages.
- Team professionalism: We have a professional technical team. We are not only able to carry out production, but also help customers find and solve key problems. In the production of military castings. Facing complex technical problems and strict performance requirements. The professional team can provide more effective technical support and solutions.
Military casting applications
Military castings are widely used in various military equipment. The following are common application scenarios and specific parts of JC Casting:
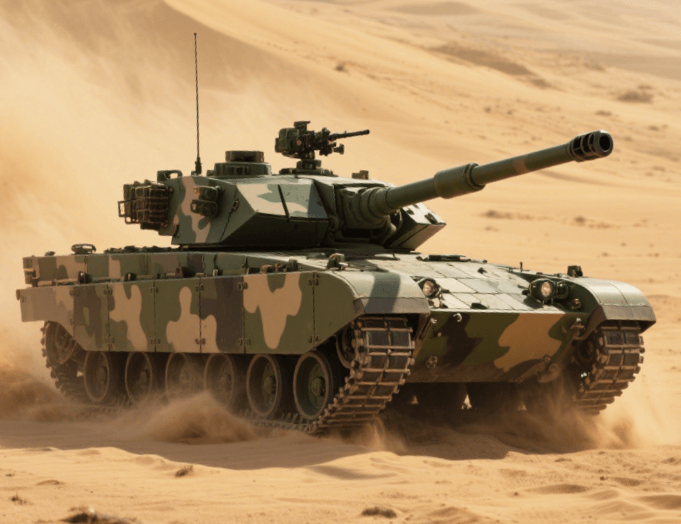
Army Equipment
- Tanks and armored vehicles: Protective armor plates, track plates, etc.
- Artillery systems: Barrel bases, shell launchers, etc.
- Military vehicles: Body frames, suspension system components, etc.
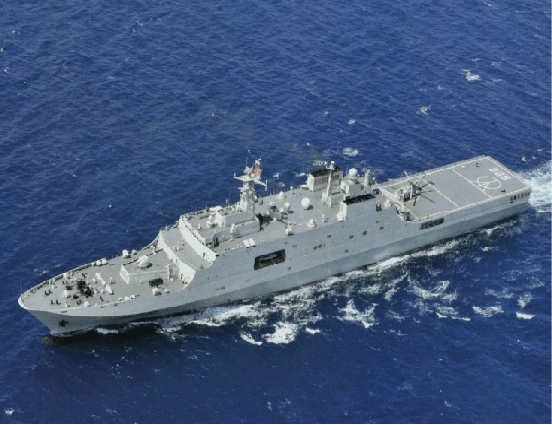
Naval equipment
- Ships: Hull structure, drive shaft housing, etc.
- Submarines: Pressure hull components, periscope brackets, etc.
- Shipborne equipment: Radar base, communication equipment housing, etc.
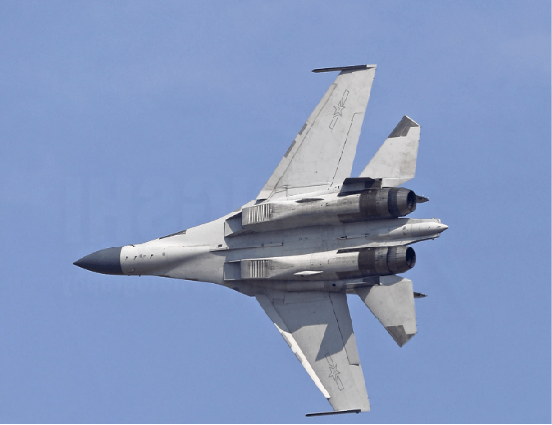
Aviation equipment
- Fighters/Bombers: Fuselage frames, wing connectors, etc.
- Helicopters: Gearbox housings, avionics housings, etc.
- Military transport aircraft: Landing gear components, hydraulic system castings, etc.
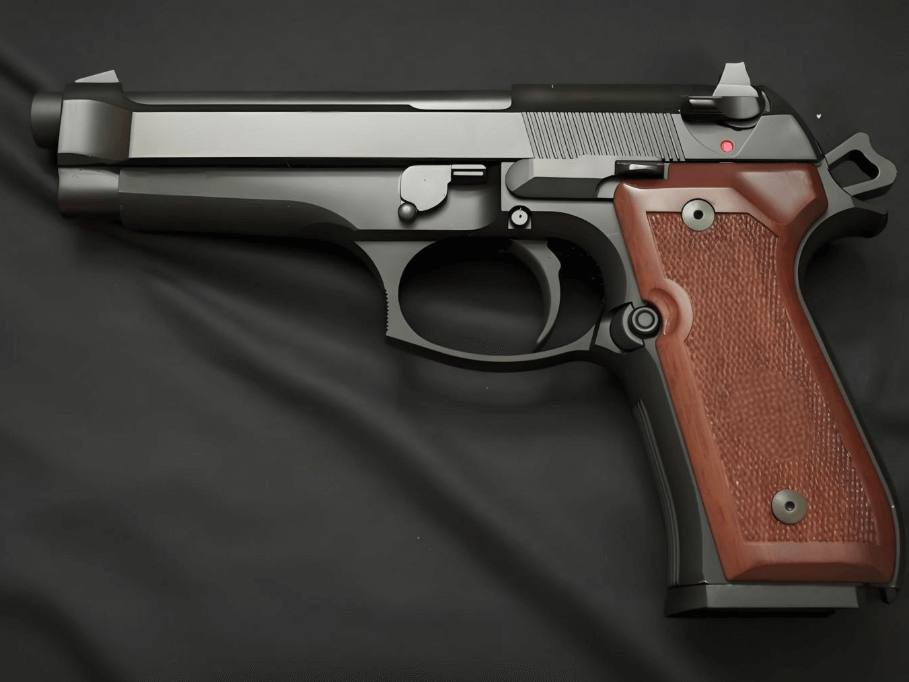
Light weapons and general equipment
- Firearms: Receivers, barrel bases, etc.
- Communications and radar: Radar waveguide components, military radio housings, etc.
- Protective equipment: Helmet lining metal frames, body armor connectors, etc.
Why cooperate with JC Casting
There are significant advantages to working with JC Casting.
In casting technology. JC Casting is proficient in investment casting. Through precision wax patterns and multi-layer refractory material processing. It can accurately shape complex parts. Such as helicopter engine blades. It ensures stability in extreme environments. The casting accuracy and surface quality can meet the stringent requirements of military equipment.
We also have rich experience in sand casting. We can produce large and complex castings such as tank structural parts and artillery bases at a reasonable cost. And by strictly controlling the sand formula and molding process. We can ensure stable and reliable quality.
In terms of service, JC Casting provides one-stop service from design to production. Professional teams communicate deeply about needs. Assist in optimizing design. Finely control quality throughout the production process. Efficiently schedule production. Ensure on-time delivery.
If you are looking for a reliable partner, please contact JC Casting! Let us escort your project!