What is Fluid Equipment Connectors
Fluid equipment connectors are used in specific systems. These systems include systems for conveying, controlling or processing fluids. Such as liquids, gases, steam, etc. Its function is to connect various equipment or components. Such as pipes, valves, pumps, etc. This is a special connection component. It is the “joint” of the fluid system. This type of casting is a key component of the fluid system. It directly affects the sealing, pressure resistance and safety of the system.
JC Casting is a caster and supplier of fluid equipment connectors. Provide customers with high-quality castings and services.
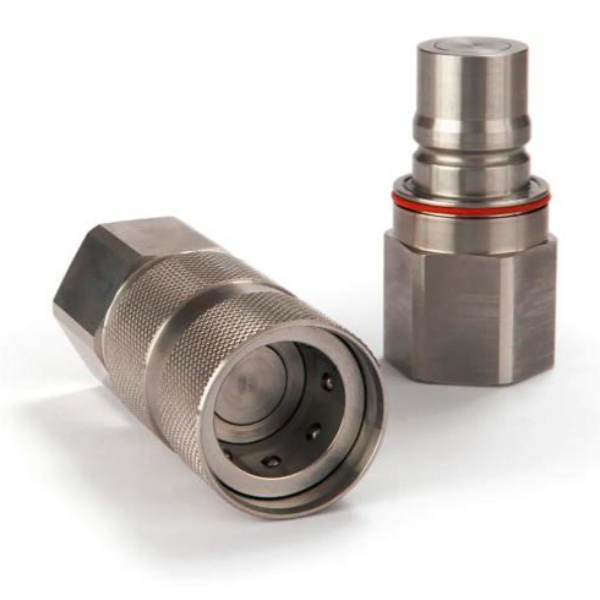
Features of fluid equipment connectors
Connectivity
Combine dispersed fluid equipment or pipeline components into a complete system. Ensure the relative position of each component is stable. Achieve fixed connection of components of different pipe diameters and types. Such as pipelines and valves, pumps and pipelines, containers and instruments, etc. Ensure that the fluid is transported along the preset path.
Sealing guarantee
The structural design and material properties must meet strict sealing requirements. To prevent fluid leakage. Especially corrosive, high-temperature and high-pressure fluids. This is usually achieved through flange surfaces, threads, sealing ring grooves and other structures.
Fluid Path Connection
Provide a continuous and unobstructed flow path for the fluid. It can be adapted to components with different pipe diameters, different directions or different connection forms. Such as right angles, three-way splitters, flanges, etc.
Adapting fluid properties
The material should be selected according to the physical and chemical properties of the fluid. Such as cast iron, cast steel, stainless steel, copper alloy, etc.
For example:
1. When conveying corrosive fluids. Stainless steel castings are often used;
2. In high-pressure steam systems. High-strength steel castings are often used.
Common casting materials for fluid equipment connectors
Category | Common materials | Features |
Cast iron | Gray cast iron | Low cost. Good wear resistance. Suitable for low pressure fluid pipeline connection. |
Ductile cast iron | The strength and toughness are better than gray cast iron. It can withstand higher pressure. | |
Cast steel | Carbon cast steel (such as ZG230-450) | High strength. Good welding performance. Suitable for high pressure fluid system. |
Alloy cast steel (such as chrome-molybdenum cast steel) | High temperature and high pressure resistance.Used for connecting high temperature and high pressure fluid equipment in chemical industry, power station, etc. | |
Nonferrous metal casting | Cast brass | Good corrosion resistant, good thermal conductivity. Suitable for conveying non-corrosive fluids. Such as water and oil. |
Special alloy casting | Stainless steel castings (such as 304, 316) | It has strong corrosion resistance. Suitable for fluid systems in chemical and food industries. Which have high requirements for cleanliness and corrosion resistance. |
Fluid equipment connector application
Fluid equipment connectors have a wide range of applications. Mainly in the following areas:
- Chemical and petrochemical industry: Acid and alkali pipe joints. Reactor interfaces.
- Energy and power industry: Steam pipe flanges. Cooling water pipe elbows.
- Municipal and water treatment industry: Tap water pipe elbows. Gas pipe joints.
- Shipbuilding and marine engineering: Cooling water pipe joints. Fuel pipe elbows.
- Food and pharmaceutical industry: Sterile water pipe joints. Tank interfaces.
- Mechanical and hydraulic systems: Hydraulic pipe joints. Machine tool pipeline interfaces.
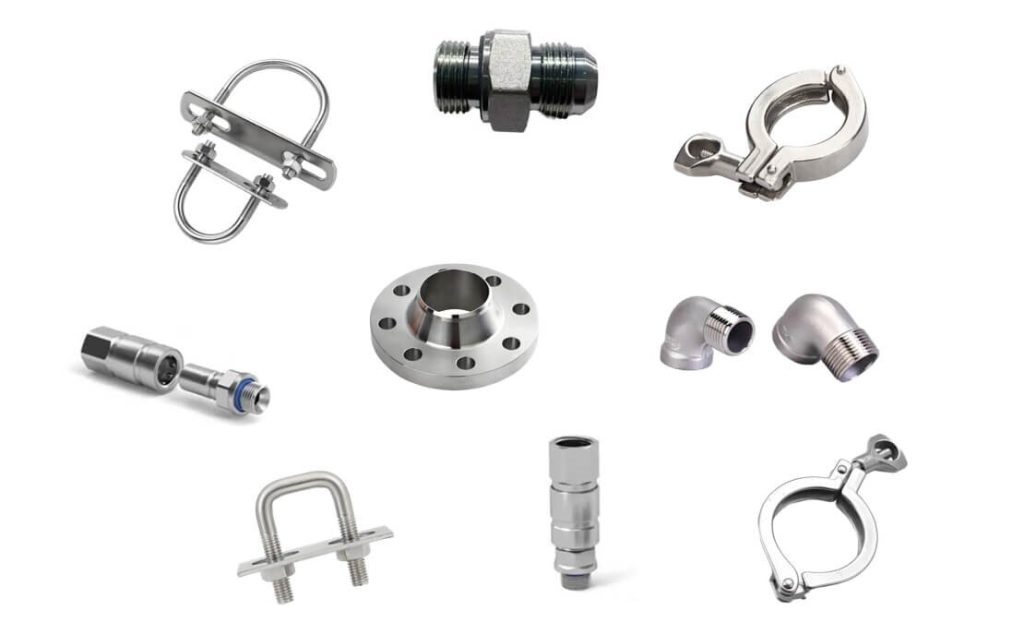
JC Casting Factory casting process
JC Casting commonly uses sand casting and investment casting processes.
Sand Casting
Process features: Sand material is used as the casting mold base. The mold cavity is formed by the mold. The molten metal is directly poured into the sand mold. After cooling, the sand mold is broken to obtain the casting. The process is simple. The sand mold formula can be flexibly adjusted to adapt to different metal materials.
Applicable scenarios: Mainly used for flanges, elbows, straight joints, etc. Made of gray cast iron, ductile iron, etc. Especially for connectors with relatively regular structures. Suitable for low-pressure fluid system components of medium and large sizes or mass production.
Core advantages: Low equipment investment. Short production cycle. Quick response to batch orders. Strong compatibility with casting sizes. Stable production from small and medium-caliber joints to large flanges.
Investment Casting
Process features: First, a wax model is made. After being coated with multiple layers of refractory materials, a high-strength shell is formed. After the wax model is melted, a precision casting is obtained. Then, molten metal is poured into the mold. The casting surface is smooth and has high dimensional accuracy. No complicated subsequent processing is required.
Applicable scenarios: Mostly used for special-shaped joints made of stainless steel and alloy materials. Suitable for fluid systems. Such as chemical industry and medicine. Which have high requirements for sealing and cleanliness.
Core advantages: Complex inner cavity or special-shaped structure can be cast. Special connection path design requirements can be met. High density of castings. Able to withstand high pressure, corrosion and other harsh working conditions. Reduce leakage risk.
The two processes complement each other. According to the material, structure and use environment of the connector. JC Casting will flexibly select the best casting solution. To ensure the balance between product performance and cost.
JC Casting Manufacturer Advantages
JC Casting has many core advantages in the field of fluid equipment connector castings.
Mature processing technology
- We have stable process systems such as sand casting and investment casting. We can flexibly adjust the process according to the material and structural characteristics of the castings. Ensure the molding quality of different types of connectors.
- Complete supporting follow-up processing procedures. Including surface cleaning, precision finishing, etc., Can reduce casting defects and improve overall performance.
Strict quality control
- There are standardized processes from raw material selection to finished product inspection. Internal and surface defects of castings are checked through intuitive testing methods. Avoid the outflow of unqualified products.
- According to the characteristic requirements of different application scenarios. Such as pressure resistance and corrosion resistance. Carry out targeted tests. Ensure that the product is suitable for actual working conditions.
Flexible customization capabilities
- We can design exclusive casting solutions according to the drawings or requirements provided by customers. And produce connectors suitable for special sizes and special-shaped structures.
- Supports customization of multiple materials. From ordinary cast iron to stainless steel and alloy materials. All can be matched with corresponding processes to complete production.
Perfect after-sales service
- Provide product usage guidance. Assist customers to solve problems that arise during installation and adaptation.
- Establish an after-sales tracking mechanism. Respond to customer feedback in a timely manner. Properly handle quality issues. Ensure customer experience.
These advantages enable JC Casting to provide fluid equipment connectors that meet industry needs. Meet the diverse demands of different customers.
Why cooperate with JC Casting
JC Casting has an independent factory and CNC processing center. The whole process of production and processing is under independent control. Intermediate links are eliminated. It can bring higher cost performance while ensuring quality. Let customers obtain reliable fluid equipment connector castings at a reasonable cost.
JC Casting has accumulated more than 20 years of casting experience. We have a deep understanding of the casting process of connectors with different materials and structures. We can accurately deal with various production problems. And ensure stable product quality from the source.
JC Casting has accumulated more than 20 years of casting experience. We have a deep understanding of the casting process of connectors with different materials and structures. We can accurately deal with various production problems and ensure stable product quality from the source.
If you are interested in fluid equipment connector projects. Welcome to cooperate with JC Casting!