What is Carbon Steel Casting?
Carbon steel is an iron-carbon alloy with a carbon content of 0.12%-2.11%. It generally also contains small amounts of SI, Mn, S, P and other elements. Its performance mainly depends on the carbon content. The higher the carbon content of carbon steel, the greater the strength and hardness. But the toughness and plasticity are lower. Carbon steel castings are parts or blanks that are formed by melting carbon steel and pouring it into a mold and cooling it. It is widely used in the manufacture of parts such as gears and cylinders that can withstand a certain load. As a leading metal casting manufacturer in China. JC Casting can provide carbon steel castings with higher quality and wear resistance.
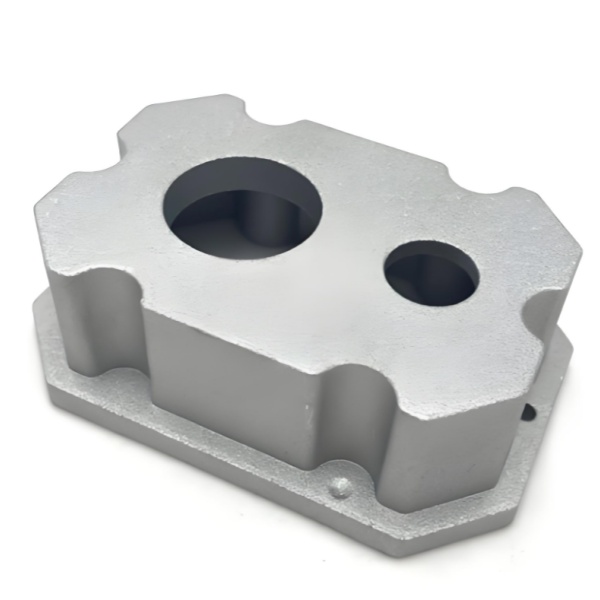
Types of Carbon Steel for Casting
Low carbon steel: Carbon content < 0.20%.
This type of steel has a very low carbon content. Good plasticity and toughness. Good ductility and weldability. But low strength and hardness. Its typical use is to manufacture parts that need to be welded, such as machine bases, automobile body panels, wire products, etc.
Medium carbon steel: Carbon content ranges from 0.20% to 0.60%.
Manganese content ranges from 0.60% to 1.65%. Good comprehensive mechanical properties. High hardness and strength. Good ductility. Can be hardened and tempered by hardening treatment to obtain high surface hardness and wear resistance. Widely used in the manufacture of parts subject to medium loads. Such as gears, crankshafts, axles and cylinder blocks.
High carbon steel: Carbon content ranges from 0.60% to 1.00%.
This type of steel has high hardness. Strong wear resistance. But poor toughness and plasticity. And low weldability. Widely used in the manufacture of wear-resistant parts. Such as rollers, springs, cams, high-strength metal wires, etc.
Features and Benefits of Carbon Steel Castings
Different types of carbon steel have different properties to suit specific needs
Features | Low carbon steel | Medium carbon steel | High carbon steel |
Strength / Hardness | Low | Medium. Can be improved by heat treatment | High. Brittle |
Plasticity / Toughness | High | Medium | Low. Significant brittleness |
Weldability | Excellent. No special process required | Poor. Preheating and slow cooling required | Very poor. Strict process control required |
Heat treatment | Annealing/normalizing improves cutting performance | Quenching and tempering (quenching + tempering) improves overall performance | Quenching + low temperature tempering improves hardness and wear resistance |
Typical applications | Stamping parts. Welded structures. Low-load parts | Medium-load parts such as gears, shafts, connecting rods, etc | Tools. Springs. Wear-resistant parts |
Due to the difference in carbon content. They show their distinct advantages in performance and application:
Low carbon steel
1. Outstanding plasticity and toughness: Not easy to break. Suitable for cold processing (such as stamping). Can be made into parts with complex shapes.
2. Excellent welding performance: Can be welded without preheating or special processes. Widely used in the manufacture of steel structures and welded parts.
3. Low processing cost: High plasticity during cutting. Small shrinkage during casting. Low process difficulty.
Medium carbon steel
1. Balanced comprehensive mechanical properties: Moderate strength, hardness and toughness. Performance can be further optimized through quenching and tempering (quenching + tempering). Meet the needs of various working conditions.
2. Excellent machinability: Moderate hardness. Slow tool wear during cutting. Suitable for manufacturing precision mechanical parts such as gears and shafts.
3. High cost-performance ratio between cost and performance: The price is lower than alloy steel. But after heat treatment, it can achieve performance close to that of alloy steel. Suitable for mass production.
High carbon steel
1. Extremely hard and wear-resistant: The hardness after quenching can reach HRC60 or above. Suitable for manufacturing cutting tools, wear-resistant linings, etc.
2. High elastic limit: Can be used to manufacture automotive leaf springs, etc. Can quickly return to its original shape after deformation.
3. Wide range of material sources: The cost is lower than that of wear-resistant materials such as cemented carbide. Suitable for scenes with high requirements for wear resistance.
Summary
- Low carbon steel: High formability and weldability. It is the first choice for low-cost, high-plasticity scenarios.
- Medium carbon steel: Balance of toughness and strength. It can be flexibly adapted to different load requirements through heat treatment.
- High carbon steel: High hardness and wear resistance. It is irreplaceable in the field of tools and wear-resistant parts.
Common Carbon Steel Alloys for Casting
In the field of casting, AISI 1018, AISI 1020, AISI 1040, AISI 1045, AISI 1080, and AISI 1095 are several common carbon steel alloys. Their main difference comes from the different carbon content. The higher the carbon content, the harder and stronger the steel is. However, the toughness will decrease accordingly. JC Casting can select the appropriate carbon steel model for customers based on their requirements for mechanical properties and specific usage scenarios.
Carbon steel alloy | Carbon content | Main features | Typical application scenarios |
AISI 1018 | 0.15% – 0.20% | Low carbon steel. Excellent plasticity and weldability. Good machinability | Auto parts, gear blanks, welding structural parts |
AISI 1020 | 0.18% – 0.23% | Low carbon steel. Excellent cold formability. Good weldability | Pipe fittings, spindles, bushings, pins, stamping parts |
AISI 1040 | 0.37% – 0.44% | Medium carbon steel. Balanced workability and wear resistance. | Gears, shafts, connecting rods, bolts |
AISI 1045 | 0.43% – 0.50% | Medium carbon steel. High strength and hardness. Excellent wear resistance | Machine tool spindles, gears, shafts, crankshafts, heavy machinery parts, gearbox housings |
AISI 1080 | 0.75% – 0.88% | High carbon steel. High hardness and wear resistance. High elastic limit. High brittleness | Springs, low-speed cutting tools, wear-resistant linings |
AISI 1095 | 0.90% – 1.03% | High carbon steel. Very high hardness. Very wear resistant. Highly sensitive to heat treatment | Hand tools, stamping dies, ball mill steel balls, wear-resistant parts |
Application of Carbon Steel Castings
Carbon steel castings are widely used in different industries due to their versatility.
- Automobile: such as automobile chassis parts, gears, axles, brake system parts, etc.
- Construction: used for bridge connectors, building fasteners, etc.
- Machinery: used to manufacture mechanical parts such as gears, shafts, crankshafts, couplings, etc.
- Agriculture: plow blades, harvester blades, etc.
- General parts: valves, flanges, pump bodies and other general industrial parts.
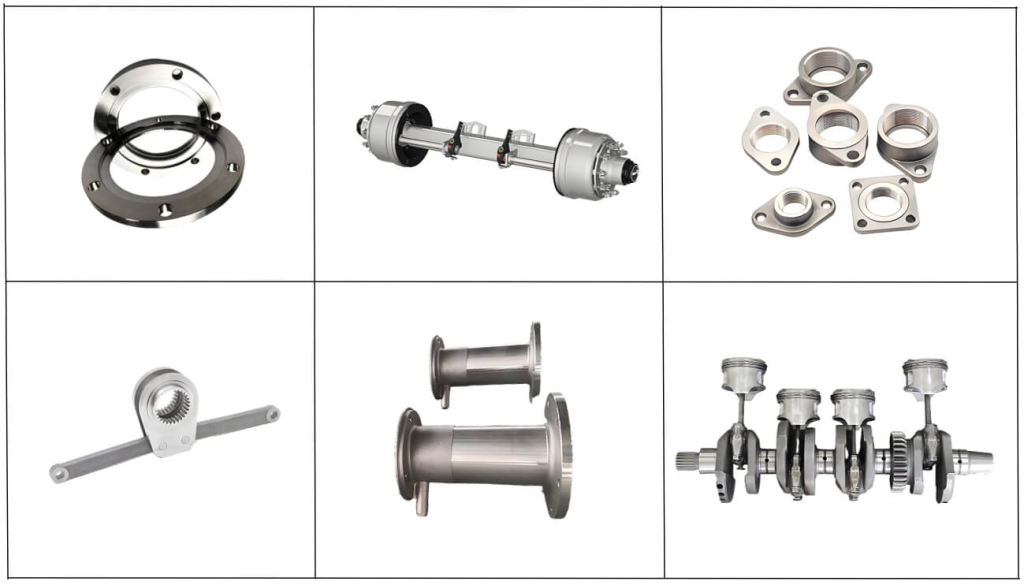
The application of carbon steel castings covers many aspects of industrial production and social life. JC Casting can flexibly meet the requirements of carbon steel for strength, toughness, wear resistance and other properties in different scenarios by adjusting the carbon content and heat treatment process.
JC Casting’s Surface Treatment Process
Surface treatment process | Introduction |
Powder Coat Finish | Powder coating is a common high-quality surface treatment process for carbon steel castings. Although it costs more than painting, it can provide a more durable coating. |
Galvanized Surface Treatment | Galvanizing is a process of coating steel castings with zinc to protect the base material from corrosion. It can enhance strength and improve working performance. |
Shot Peening | Shot blasting is a commonly used surface finishing method for carbon steel castings. The principle is to spray small steel balls onto the surface of the casting to remove impurities and burrs to obtain a clean and smooth surface. |
Painted Finish | Painting is an economical surface treatment for carbon steel castings. There are many colors to choose from. It can prevent parts from rusting for a long time. |
Machining Surface Treatment | When some areas of carbon steel castings do not meet the dimensional tolerance or surface finish requirements of the drawing, surface processing is required. JC Casting has an independent factory and CNC center. It can meet various processing needs. |
Black Oxide Finish | Black oxide is a conversion coating process for carbon steel castings. It creates a black, smooth surface. Improves corrosion and wear resistance. |
Why choose to cooperate with JC Casting?
As a professional steel foundry. JC Casting has more than 20 years of experience in carbon steel casting. We are currently one of the largest carbon steel casting manufacturers in China.
As a caster of carbon steel castings. We have our own independent factory and advanced production equipment, as well as multiple production lines. We provide customers with one-stop service and customized production projects. Compared with other steel foundries, we have absolute advantages. We are both the source factory of carbon steel castings. We are also an exporter and supplier for many years. We are able to supply small and large batches of cast steel parts. And provide a series of value-added services and surface processing services. Such as polishing, machining, heat treatment, etc. JC Casting focuses on tight tolerances and complex designs. Provide a variety of grades that meet AMS, MIL and ASTM.
If you are interested in using carbon steel castings in your project. Please contact us to discuss your requirements! As a casting expert, we can provide you with the best solution for carbon steel castings!
FAQ
1. How do you ensure the quality of carbon steel products?
JC Casting strictly follows international standards for production. From raw material procurement, casting process to finished product inspection. Every link is strictly controlled by professionals. We are equipped with independent advanced testing equipment. Comprehensive testing of carbon steel products to ensure that product quality meets standards.
2. Can you customize carbon steel products?
Absolutely. We have a professional technical team and independent factories and CNC centers. We can customize production according to the drawings or samples provided by customers. We can accurately meet various dimensional tolerances, surface finish and other requirements. We ensure that customized products meet customer expectations.
3. Is there a big price difference between different surface treatment processes?
The prices of different surface treatment processes will vary due to factors such as materials and process difficulty. For example, although powder coating is more expensive, the coating is more durable. Painting is a more economical surface treatment method. We will provide you with a detailed quotation plan based on the process you choose and the order quantity.
4. Does the product provide after-sales technical support?
We adopt one-stop service. Provide customers with comprehensive after-sales technical support. If you encounter any problems during use, you can contact JC Casting’s technical team at any time. We will provide you with solutions through email, phone or remote assistance.