What is Aerospace Castings?
Aerospace castings are metal or alloy parts made by casting. These parts are mainly used in the aerospace field. Their application range includes aircraft, rockets, satellites, missiles and other aircraft and related equipment. These castings are the core components of aerospace equipment.
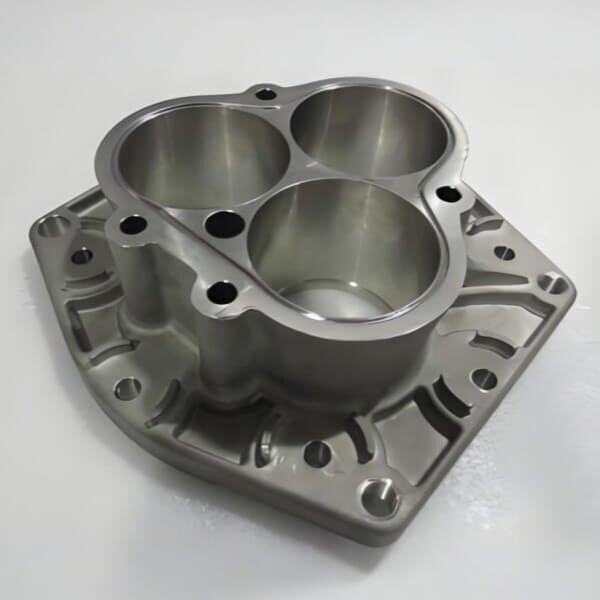
Core Features of Aerospace Castings
High strength and light weight: It must meet extreme loads. And reduce weight as much as possible. Common materials include titanium alloy, aluminum alloy, high temperature alloy, etc.
High temperature resistance and corrosion resistance: In engine combustion chambers, rocket nozzles and other parts. They need to withstand thousands of degrees Celsius of high temperature. In the atmosphere or in space. They need to resist corrosion such as oxidation and radiation.
High precision and low defects: No tiny defects such as pores and cracks are allowed inside the casting. The dimensional tolerance must be controlled at the micron level.
Why choose casting process
Compared with other processes. Casting can more accurately adapt to the stringent requirements of parts in this field.
Adapt to complex structures
Aviation parts often contain complex structures. Such as special-shaped curved surfaces and hollow cavities. And need to integrate multiple functions. Casting can form such structures in one piece. And reduce the number of splicing welds.
Overcoming the challenges of processing high-performance materials
Castings are mostly made of high-strength materials. Such as titanium alloys and high-temperature alloys. These materials have high hardness and high melting points. The tool wears quickly during machining. The efficiency is extremely low. Forging is also prone to cracks. Casting directly fills the mold with molten metal. It can avoid the technical bottleneck of material processing.
Ensure the uniformity of material properties.
Meeting performance requirements in extreme environments
Aircraft parts need to withstand extreme working conditions. Such as high temperature and high pressure. Casting can reduce defects. Such as pores through vacuum casting and other technologies. So that the high temperature resistance and fatigue resistance of parts can fully adapt to the requirements of extreme environments.
Balancing cost and efficiency
For expensive special alloys. The casting material utilization rate reaches 50% or more. It is much higher than other processing technologies. It can reduce waste. For complex parts produced in batches. Casting can achieve efficient molding through repeated use of molds. Reduce processing and assembly costs.
Common aviation casting materials and processes
Casting materials
High temperature alloy
It is the core material of engine turbine blades and combustion chambers. It can maintain high strength, creep resistance and corrosion resistance at high temperatures of 600-1200℃. Typical alloys such as nickel-based high-temperature alloys, can accurately control the grain structure through the casting process. It can meet the extreme working conditions of the engine.
Titanium Alloy
High strength. Low density. Excellent corrosion resistance. Widely used in aircraft fuselage frames, landing gear and other parts. Its castings can reduce the weight of the aircraft. Ensuring structural strength. It is a key material to achieve “lightweight”.
Aluminum Alloy
Low cost. Good processing performance. Suitable for manufacturing cabin structures, satellite brackets and other non-load-bearing or medium-low load parts. Thin-walled parts with complex shapes can be mass-produced through casting. It takes into account both lightness and economy.
Magnesium Alloy
Lighter than aluminum alloy. Often used in lightweight structural parts of spacecraft. Such as satellite antenna brackets and missile compartments. Since magnesium is easily oxidized. Its corrosion resistance needs to be improved through casting technology.
Casting process
JC Casting typically uses methods such as investment casting and vacuum casting to cast aerospace castings.
Investment Casting (Lost Wax Casting)
Principle: Use wax to make a prototype of the part. Apply multiple layers of refractory material to form a shell. After melting the wax pattern. Inject the molten metal into the shell to form the part.
Advantages: It can manufacture complex parts with extremely high precision (dimensional tolerance can reach ±0.1mm) and smooth surface. Such as cooling channels of turbine blades. It is especially suitable for difficult-to-process materials such as high-temperature alloys.
Vacuum Casting
Principle: Melt the metal in a vacuum environment and pour it. Avoid mixing gas into the molten metal.
Advantages: Significantly reduce defects. Such as pores and inclusions in castings. Improve material density. Suitable for casting easily oxidized materials. Such as titanium alloys and high-temperature alloys.
JC Casting Aerospace Casting Applications
Aircraft engines: Turbine blades. Turbine discs, etc.
Spacecraft: Rocket engine nozzles. Satellite load-bearing frames, etc.
Aircraft bodies: Fuselage beams. Landing gear shock absorber struts, etc.
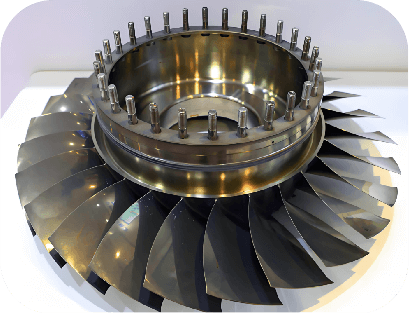
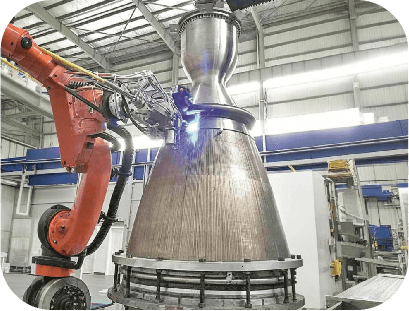
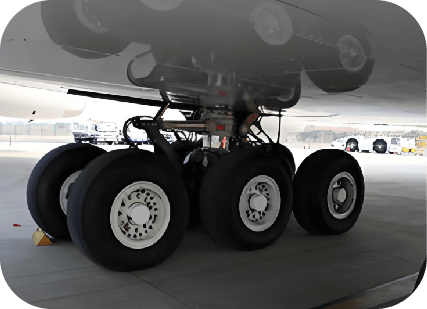
Partner with JC Casting
In the field of aerospace castings. JC’s customization capabilities are particularly outstanding. According to the different flight environments and structural loads of aircraft and spacecraft. We can accurately achieve deep customization from design to production. We also cover the manufacture of special castings. Such as complex cavities and thin-walled structures.
In terms of quality control. JC Casting uses high-precision non-destructive testing. Such as eddy current and penetration. To fully guarantee the quality of castings. Facing harsh working conditions. Such as high altitude, low air pressure, and extreme temperature differences. JC Casting uses super alloy materials and investment casting and vacuum casting technology. To create lightweight, high-strength, high-temperature-resistant, and fatigue-resistant castings. Effectively improving the operational reliability of aerospace vehicles. And reducing the risk of failure and maintenance costs.
Cooperate with JC Casting. To enjoy professional one-stop aerospace casting services. If you have any needs, please contact JC Casting.