The brake disc is a key component to ensure driving safety. It works with the brake pad. Braking force is generated through friction. This allows the vehicle to slow down or stop. QD has accumulated rich experience in the production and manufacturing of brake discs. Provide high-quality brake disc products and services.
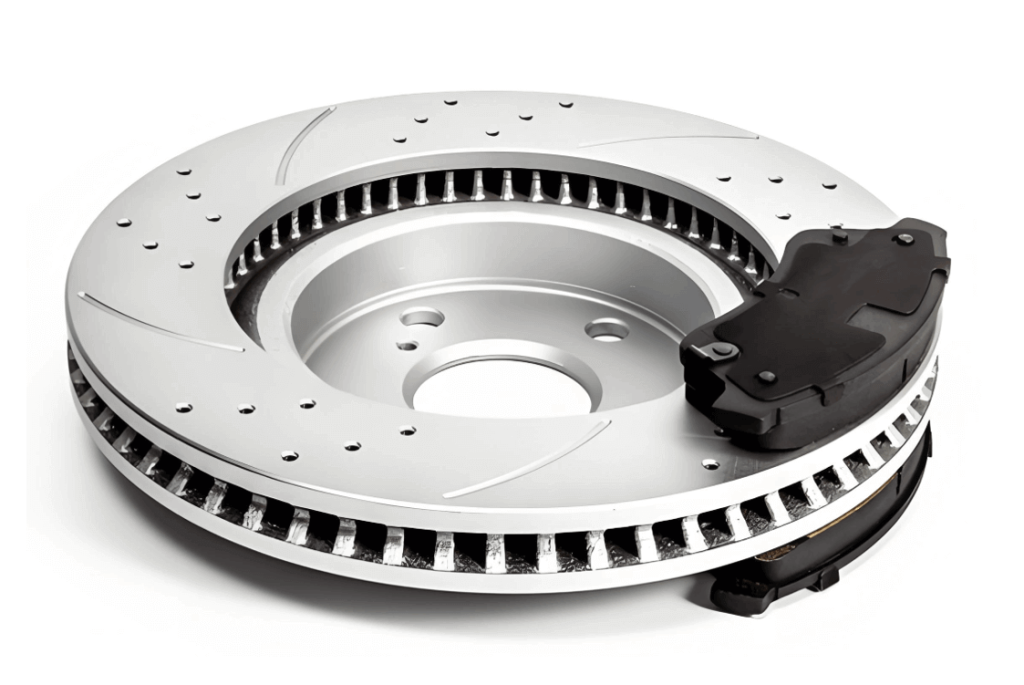
Function of brake disc
The main function of brake disc is to work with brake pads. When the driver steps on the brake pedal, friction is generated through the close contact between the two. The kinetic energy of the car is converted into heat energy. The vehicle is decelerated or stopped.
- Ensure braking efficiency: High-quality brake discs can ensure that the vehicle can decelerate quickly and stably under various road conditions. Shorten the braking distance.
- Improve driving safety: In emergency braking scenarios, reliable brake discs can avoid dangerous situations such as brake failure.
- Extend the life of the braking system: Good brake disc materials and processes can reduce wear and tear on the brake pads. Extend the service life of the entire braking system.
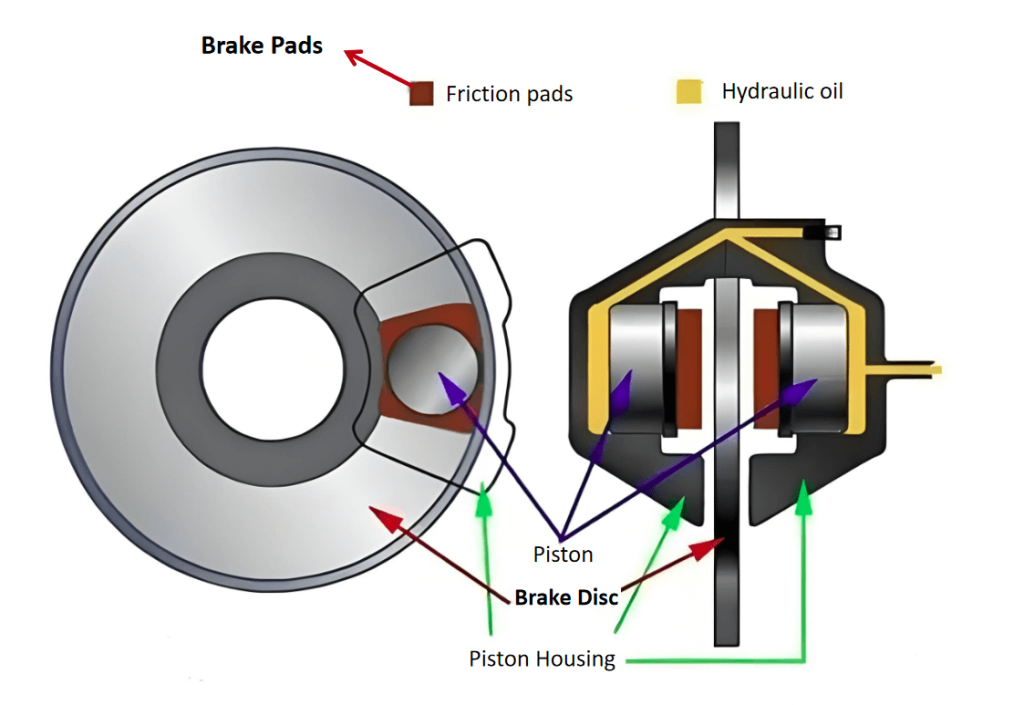
Common materials
Gray cast iron: It is one of the most commonly used casting materials for brake discs. It has good wear resistance and thermal conductivity. It can quickly dissipate heat during braking. It avoids the degradation of braking performance due to high temperature. Common models include HT250 and HT300.
- HT250: It has high strength and hardness. Can meet the braking needs of ordinary family cars. Excellent cost performance.
- HT300: It’s superior to HT250 in strength and wear resistance. Suitable for vehicles that often drive on complex road conditions or have higher requirements for braking performance.
Ductile iron: Compared with gray cast iron, it has higher strength and toughness. It is more stable when subjected to large braking loads. It is suitable for vehicles with higher braking performance requirements.
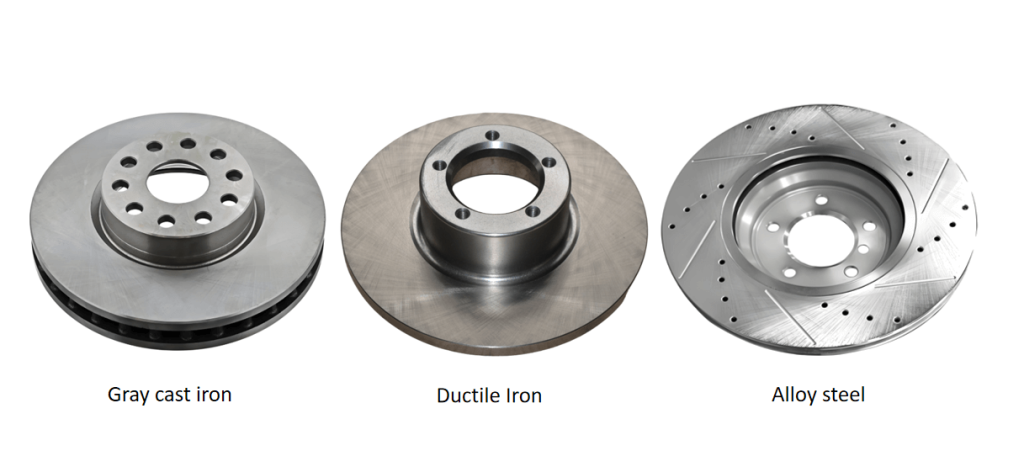
Advantages of QD brake discs
- Wear-resistant: Made of high-quality cast iron. Can withstand long-term friction loss. Can maintain a stable wear rate under frequent braking conditions. The service life can reach several years. Far superior to ordinary brake discs.
- Good heat dissipation: Combined with excellent material properties, the brake disc structure design is optimized. Ensure that the heat generated by the brake disc during braking can be quickly dissipated. Avoid brake decay due to overheating. Maintain stable heat dissipation performance.
- Stable braking: Under different vehicle speeds and road conditions, the QD brake disc and brake pad fit very tightly and evenly. Maintain a stable braking effect. Reduce vibration and noise during braking. Improve driving comfort.
- Strong adaptability: According to the braking system requirements of different models, brake discs of various specifications can be customized and produced. Whether it is a small family car, a large truck, or a special operation vehicle. QD brake discs can match a variety of brake pad types. Meet the installation and use requirements of various vehicles, without customers worrying about adaptation issues.
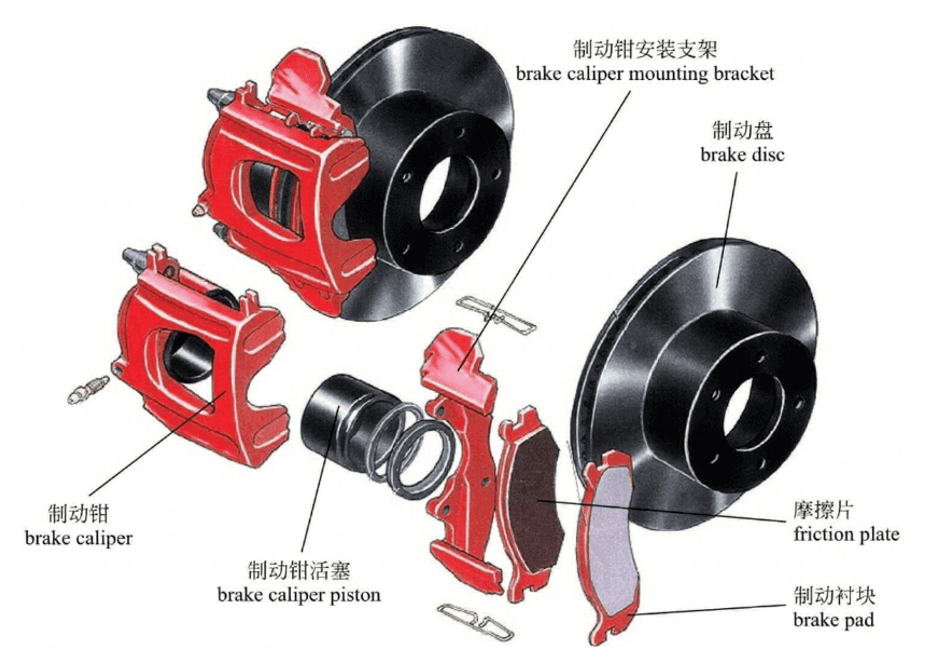
Sand casting process and procedures
QD mainly uses sand casting process in the production of brake discs.
- Mold making: Make the mold according to the design drawings of the brake disc. Ensure the mold size is accurate.
- Sand mold making: Fill the mold with molding sand. After compaction, a sand mold is formed.
- Melting: Melt raw materials such as cast iron at high temperature. Make it into molten metal that meets the requirements.
- Pouring: Pour the molten metal into the sand mold. After it cools and solidifies, it forms a brake disc blank.
- Sand removal and cleaning: Remove the molding sand and excess pouring risers on the surface of the casting. Get a preliminary brake disc casting.
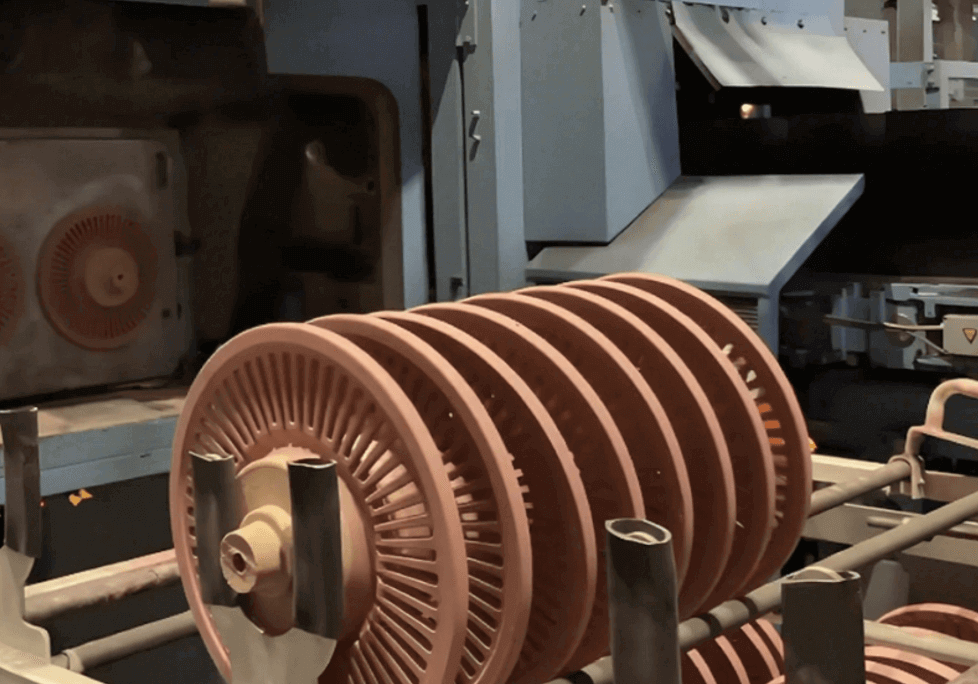
Post-treatment process of brake disc
QD has comprehensive post-processing capabilities. After casting, we provide a variety of post-processing services for brake discs:
Process Type | Specific method | Improvement of brake disc |
Heat Treatment | Annealing, quenching, etc. | Adjust the internal structure of the brake disc. Improve hardness and toughness. Enhance wear resistance and impact resistance. |
Surface treatment | Painting, phosphating, etc. | Effectively prevent the brake disc from rusting. Improve the appearance. Form a protective film on the surface of the brake disc to enhance its corrosion resistance. |
Machining | Turning, grinding, etc. | The surface and size of the brake disc are precisely processed to meet the requirements of installation and use, ensuring stability and reliability during braking. |
For example, after quenching the brake disc, the hardness is significantly improved. It can better withstand the friction during braking. Through painting, the brake disc can be made neater and prevented from corrosion during use.
Quality testing standards and cooperation advantages
QD has strict quality inspection standards for each batch of brake discs. From the raw materials entering the factory to the finished products leaving the factory, every link is carefully inspected. Every brake disc produced will be 100% dynamic balance tested. Ensure that the performance and size of the brake disc meet the relevant standards.
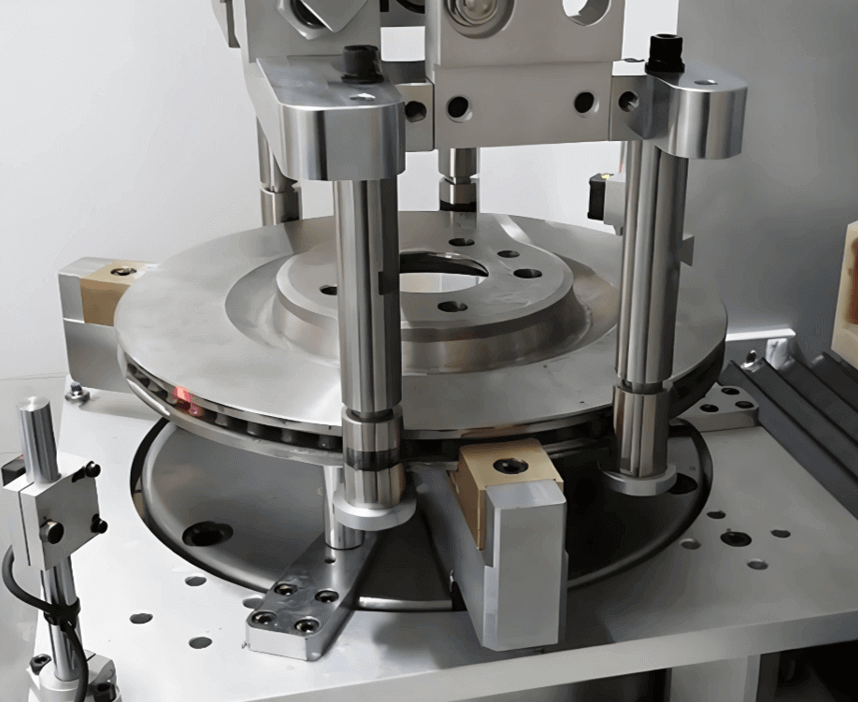
Advantages of cooperation
- One-stop service: QD not only independently completes the casting process of brake discs, but also provides one-stop post-processing services including heat treatment, surface treatment, machining, etc. Customers do not need to connect with multiple suppliers.
- Professional and reliable: QD has more than 20 years of casting experience. It has its own independent factory, advanced production equipment and multiple production lines. It focuses on a variety of casting processes and processing technologies. It provides customers with professional and reliable brake disc products.
- Meet diverse needs: QD can produce brake disc products that meet the requirements according to the different needs of customers. Meet the diverse needs of the auto parts industry.
QD provides customers with high-quality auto brake disc products with professional casting technology, perfect post-processing capabilities and strict quality inspection standards. Choose QD, choose safety and efficiency.