In casting, the molding of castings is only the first step in the manufacturing process. In order to make the castings have better performance and more beautiful appearance, post-processing technology plays a vital role. QD can provide one-stop post-processing services. Greatly improves the efficiency of cooperation.
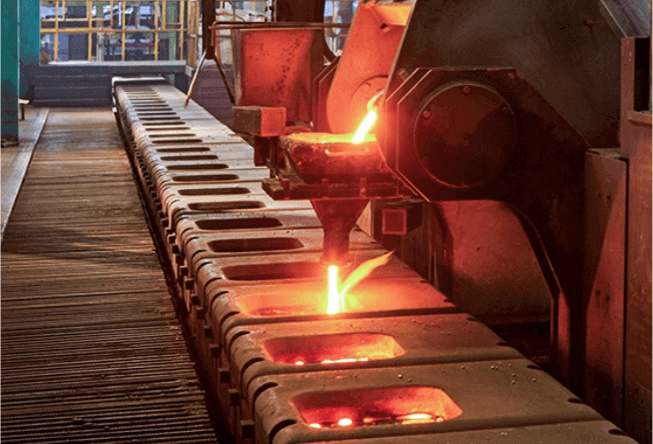
Heat treatment process
Heat treatment: heating, heat preservation and cooling of castings. Changing the microstructure inside the castings. Optimizing performance. Heat treatment can significantly improve the strength, hardness, toughness and other properties of castings.
- Annealing: Effectively eliminate the internal stress generated by the casting during the casting process. Improve the processing performance of the casting. Make the casting less likely to deform during subsequent processing. For some castings with complex shapes and high precision requirements. Such as pump and valve components and fluid equipment connectors produced by QD. Annealing is an indispensable link.
- Quenching: Can greatly improve the hardness and wear resistance of the casting. Allow the casting to maintain good performance under high pressure and friction. For example, after quenching, the hardness of steel castings can be significantly improved. Suitable for auto parts and agricultural machinery accessories with high strength requirements.
- Tempering: Usually used in conjunction with quenching. It can eliminate the internal stress caused by quenching while maintaining a certain hardness. Improve the toughness of the casting. Avoid the casting from breaking due to excessive brittleness.
- Normalizing: Heat the casting to above the critical temperature and air cool it. It can refine the grains and make the structure uniform. Improve the cutting performance and mechanical properties of the casting.
- Aging treatment: Mainly for castings such as aluminum alloys and magnesium alloys. By placing it at room temperature or under heating conditions for a period of time. Make the internal structure of the casting stable and improve dimensional stability.
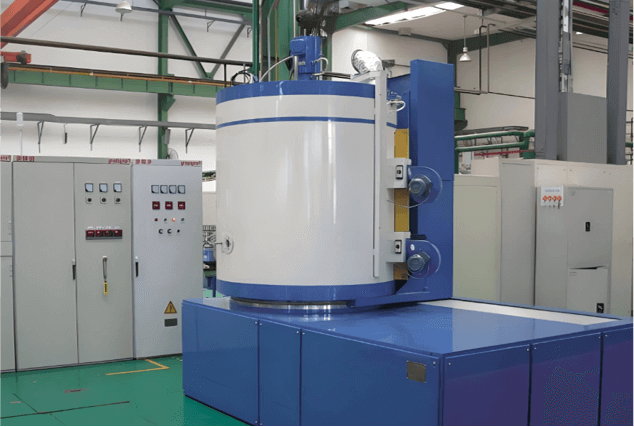
Surface treatment process
Surface treatment process: Form a protective film on the surface of the casting or change the surface state. Improve the corrosion resistance and wear resistance of the casting. Improve its appearance and texture. QD can provide a variety of treatment solutions according to the needs of different castings.
- Electroplating: Deposit a metal coating on the surface of the casting through electrolysis. Such as zinc plating, chrome plating, etc. Make the surface of the casting brighter and more beautiful. Effectively isolate the erosion of the external environment. Improve the corrosion resistance of the casting. Like some building parts and marine hardware accessories produced by QD. After electroplating, it can maintain good condition in a humid and dusty environment.
- Spraying: Apply the paint evenly on the surface of the casting to form a firm coating. Various colors can be formulated according to needs. Beautify the appearance of the casting. Play a role in corrosion and wear resistance. Suitable for products such as auto parts, agricultural machinery accessories, etc. that need to be frequently exposed to the outdoors or in complex working conditions.
- Anodizing: Mainly suitable for aluminum alloy castings. A layer of oxide film can be formed on the surface. This oxide film has high hardness and good adsorption. It can enhance the corrosion resistance and wear resistance of the casting. Provide a good foundation for subsequent coloring.
- Phosphating: A layer of phosphate film is formed on the surface of the casting. Improve the adhesion of the casting surface. Lay a good foundation for subsequent spraying, painting and other processes. Play a certain anti-rust role.
- Sand blasting: Use the impact of high-speed sand flow to clean and roughen the surface of castings. It can remove impurities such as oxide scale and oil on the surface. Make the surface uniformly rough. It is convenient for subsequent coating adhesion. It is suitable for surface treatment of various materials such as stainless steel and cast iron.
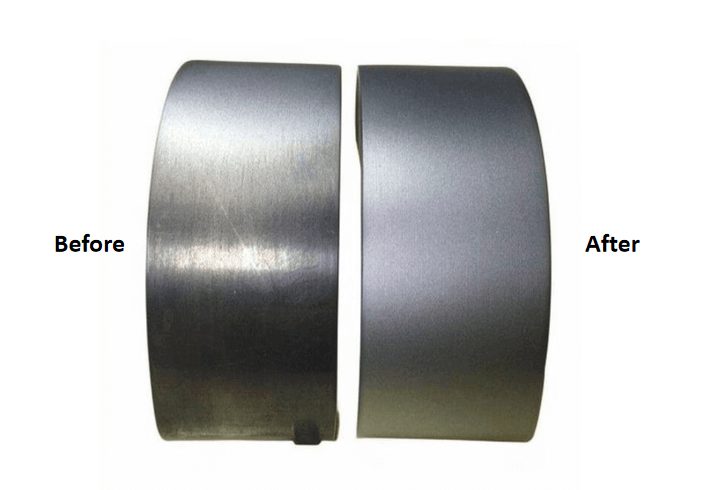
Machining Technology
After the casting is formed, its dimensional accuracy and surface roughness may not directly meet the assembly or use requirements
It needs to be trimmed by machining. QD has advanced production equipment and a professional technical team. Provide precise machining services for castings.
- Turning: Mainly used for machining rotating parts. It can cut the outer circle, inner hole, end face, etc. of the casting. It can achieve the specified dimensional accuracy and surface finish. For example, the pump and valve parts produced by QD. The flatness of its sealing surface can be guaranteed through turning. Ensure the sealing performance of the equipment.
- Milling: It can process surfaces with complex shapes such as planes, grooves, and special-shaped surfaces. It is suitable for the machining of various non-rotating castings. It can accurately machine the required structural shape.
- Grinding: It is a high-precision processing method that can further improve the surface finish and dimensional accuracy of castings. It can even achieve a mirror effect. It is suitable for aviation and medical fields that require extremely high surface accuracy.
- Boring: It is mainly used to process the hole system of large castings. It can correct the hole position deviation generated during the casting process. It ensures the dimensional accuracy and coaxiality of the hole. It is often used in the processing of machine tool bed and box castings.
- Polishing: Remove minor flaws on the casting surface by mechanical or chemical methods. Make the surface smoother and brighter. Improve the appearance and texture. Reduce fluid resistance. Applicable to products in contact with fluids, such as pump and valve parts, food machinery accessories, etc.
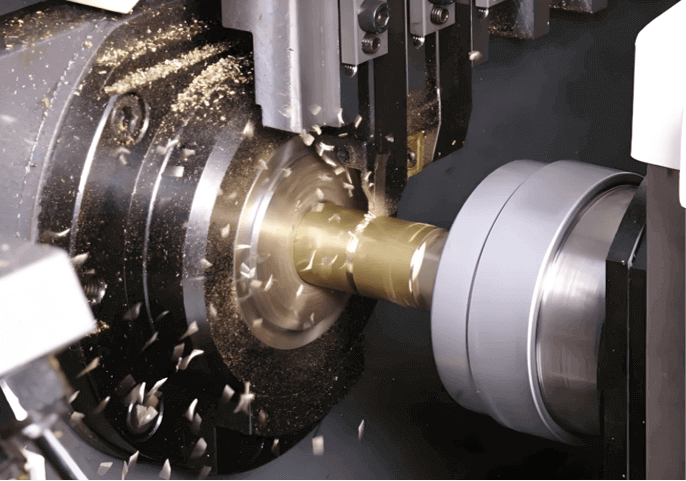
QD : One-stop post-processing service
QD provides customers with one-stop services from casting to post-processing.
Whether it is an aluminum alloy casting that needs anodizing to enhance corrosion resistance, or a steel casting that needs heat treatment to improve hardness; whether it is a simple turning process or a complex surface spraying, QD ensures the quality of each process.
Through one-stop post-processing services. QD allows customers to avoid running back and forth between the foundry and multiple post-processing suppliers. It greatly saves time and communication costs. It significantly improves cooperation efficiency. Choose QD to make the casting production worry-free throughout the process.
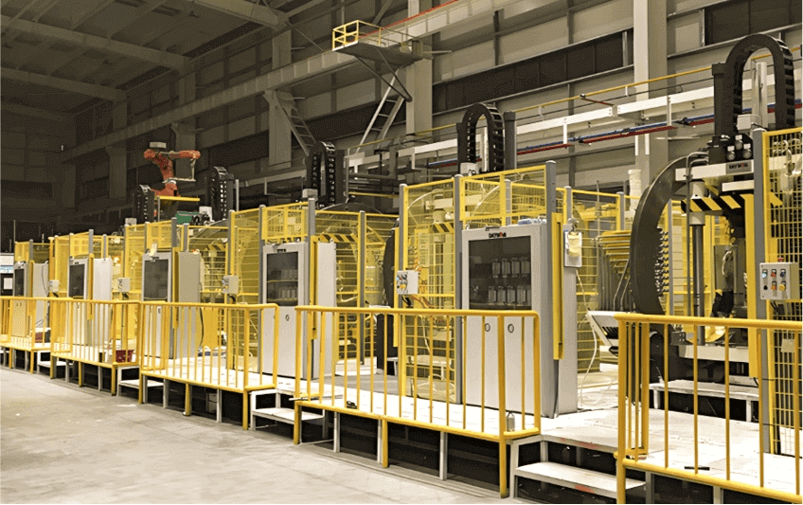