QD is a manufacturer with more than 20 years of professional casting experience. It has established a complete system that is at the forefront of the industry in the field of quality control.
Full process quality control: from source to finished product
Raw material inspection: the first line of defense for casting quality
The purity and composition stability of raw materials are the basis of casting quality. Quality control needs to cover three categories: metal furnace charge, molding materials (sand, binder), and auxiliary materials (inoculant, spheroidizer, etc.)
- Metal furnace materials need to be verified by spectral analysis to see if the composition meets the standards. Prevent problems such as mixed materials and excessive impurities.
- Modeling materials need to be tested for particle size, air permeability, strength and other indicators. Avoid sand sticking to castings due to too fine sand particles. Or insufficient air permeability causes pores.
- Auxiliary materials need to check the production date and shelf life. Prevent deterioration from affecting the smelting effect.
QD has established a strict supplier screening mechanism and factory inspection process. Ensure that each batch of raw materials undergoes multiple verifications.
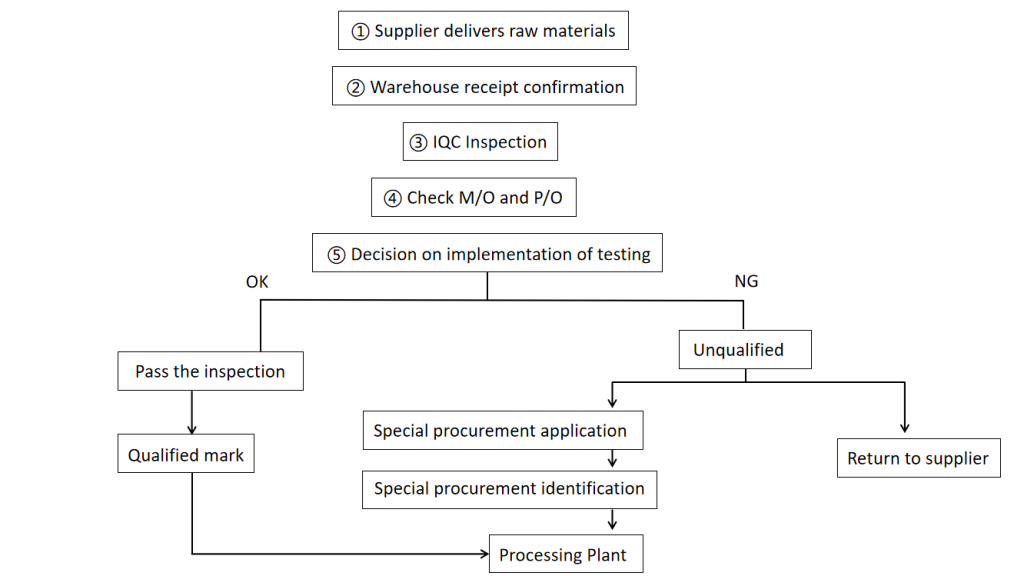
Mold design and manufacturing: the core link that determines the accuracy of castings
The rationality of mold design and processing accuracy will directly affect product size, surface quality and production stability:
- During the design phase, the solidification process of the casting needs to be simulated. The runner layout and riser setting need to be optimized. Defects such as shrinkage and deformation need to be avoided.
- During the manufacturing phase, the cavity size tolerance needs to be ensured through precision machining. At the same time, the mold surface needs to be hardened to extend the service life;
- During the mold trial phase, multiple batches of samples need to be produced continuously to verify the stability of the mold under different working conditions.
QD introduces 3D modeling and simulation technology in this process. Combined with an experienced team of engineers. We ensure that the mold design meets the product performance requirements and is suitable for mass production needs.
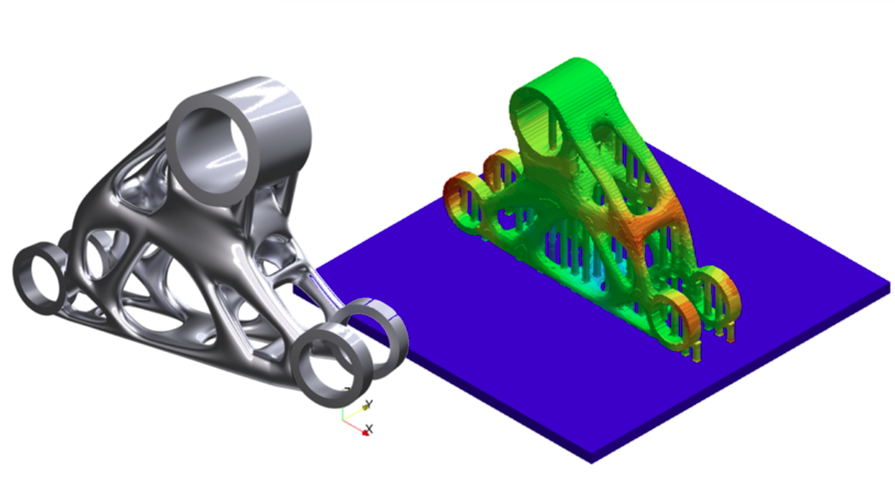
Melting and pouring: key steps to control the quality of molten metal
Melting and pouring are the core processes of converting raw materials into castings. The following factors need to be controlled:
- Melting temperature: Too high temperature will cause metal oxidation and burning. Too low temperature will result in insufficient fluidity. Real-time temperature measurement and automatic temperature control are required to maintain stability.
- Composition adjustment: Accurately add alloy elements and stir evenly according to the performance requirements of the casting. Avoid composition segregation.
- Casting process: Control the pouring speed and filling pressure. Prevent metal splashing, slag rolling or incomplete filling.
QD uses advanced testing equipment to analyze the composition and purity of molten metal. Combined with an automated pouring system, it ensures that every pouring meets process standards, fundamentally reducing quality problems caused by smelting defects.
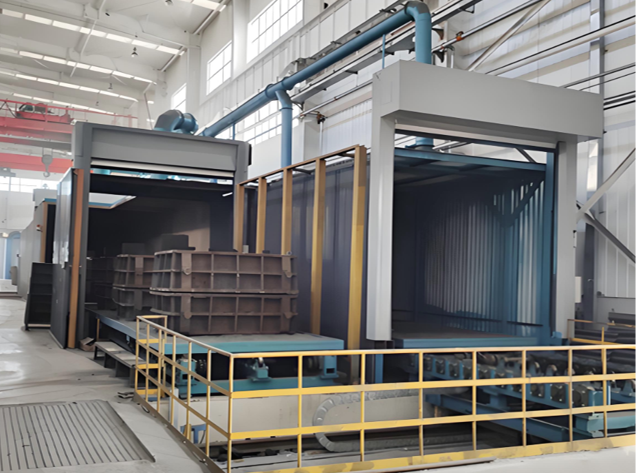
Casting cleaning and post-processing: the finishing process to improve appearance and performance
After the casting is formed, it needs to go through cleaning, heat treatment, surface treatment and other steps. The key points of quality control include:
- Cleaning stage: Avoid damaging the casting body when removing the pouring head, burrs and flash. At the same time, detect surface cracks by means of magnetic particle inspection.
- Heat treatment: Strictly control the heating rate, holding time and cooling method. Ensure that the mechanical properties of the casting meet the standards.
- Surface treatment: Select spray painting, galvanizing or anodizing processes according to needs. The surface oil and oxide scale must be thoroughly removed before treatment.
QD adopts assembly line operation and full inspection mode in the cleaning and post-processing stages. Through standardized processes, the appearance and performance consistency of each casting is guaranteed, meeting customers’ stringent requirements for product details.
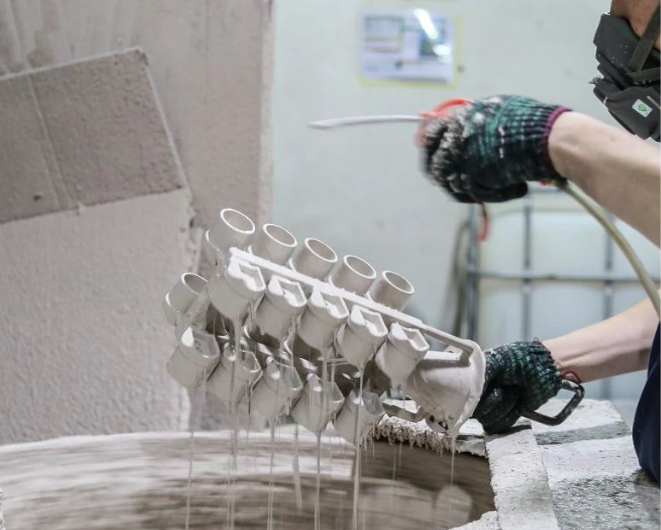
Causes and preventive measures of common casting defects
The following are solutions to common defects:
Defect Type | Main causes | Precautions |
Porosity | The gas content of the molten metal is too high. The air permeability of the molding material is poor. The pouring speed is too fast | Fully degas during smelting. Optimize the air permeability of the sand mold. Control the pouring rhythm |
Sand holes | Insufficient strength of the molding sand leads to sand falling. Incomplete cleaning of the mold cavity leaves impurities | Improve the bonding strength of the molding sand. Strengthen the cleaning of the mold cavity. Use filter sheets to block slag |
Shrinkage cavity | Uneven wall thickness of casting. Unreasonable riser design. Too fast cooling speed | Optimize casting structure to reduce wall thickness difference. Add risers to compensate for shrinkage. Control cooling gradient |
Cracks | Stress concentration during casting cooling. Improper alloy composition. Excessive temperature difference in mold | Improve casting structure to avoid sharp corners. Adjust alloy composition. Use stepped cooling |
Sand sticking | The sand mold is not refractory enough. The pouring temperature is too high. | Use high-refractory sand. Reasonably reduce the pouring temperature |
QD uses advanced testing equipment to conduct 100% inspection on castings to ensure that defects are completely eliminated before leaving the factory.
QD: Meeting the dynamic needs of customers
Quality control in the foundry industry not only relies on the management of a single link, but also requires systematic support for the entire process. With years of technical accumulation, QD has built a full-chain quality control system covering “raw materials – molds – smelting – post-processing”:
- At the standard level, all processes are implemented in accordance with international advanced standards. At the same time, the inspection plan can be customized according to customer needs;
- At the technical level, advanced means such as AI visual inspection and non-destructive testing are introduced to achieve efficient and accurate defect identification;
- At the personnel level, a quality control team with both theoretical and practical experience is cultivated to ensure that there are people responsible for each link and there are standards to follow
This all-round quality control capability enables QD’s products to not only meet the reliability requirements of traditional industries, but also adapt to the high-precision demands of emerging fields such as new energy and precision instruments.
Conclusion
QD has been deeply involved in the industry for more than 20 years and has proved that only by establishing a full-process control system from source to finished product, supplemented by advanced technology and professional teams, can the continuous stability of casting quality be achieved.