Different casting materials have different compositions and properties. They are used in different scenarios. Their selection directly affects the performance, cost and service life of the product.
Characteristics and applications of common casting materials
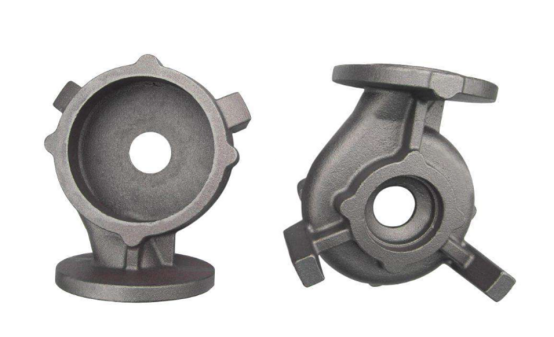
Cast iron
Cast iron is an iron-carbon alloy with a high carbon content. It has good casting properties and good fluidity. It is easy to form complex structural parts. Its main characteristics include:
- High compressive strength. But poor plasticity and toughness. Large brittleness.
- Excellent wear resistance. Suitable for making parts subject to friction.
- Relatively low cost. High cost performance.
The application scenarios of cast iron are mostly concentrated in the field of mechanical manufacturing. Such as machine tool beds, engine cylinders, pipe fittings, etc. These parts have certain requirements for pressure resistance and wear resistance. And the plasticity requirements of the material are not high.
QD can accurately control the molding quality of cast iron parts through processes such as sand casting. Meet the needs of industries such as construction and agricultural machinery.
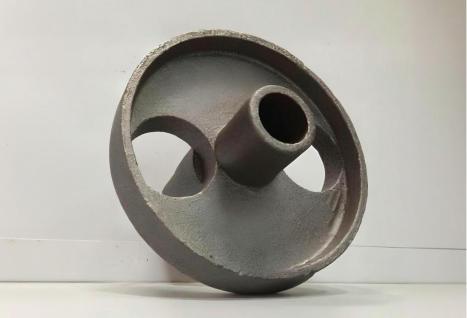
Cast steel
Cast steel is an iron-carbon alloy with a low carbon content. Different properties can be obtained by adjusting the alloying elements. Its characteristics are as follows:
- Higher strength and toughness. The comprehensive mechanical properties are better than cast iron.
- Good welding performance. Convenient for subsequent processing and assembly.
- Casting performance is slightly inferior to cast iron. Poor fluidity. It is difficult to form complex structural parts.
Cast steel is suitable for scenes with impact loads and high strength requirements, such as large gears, crane hooks, bridge components, etc. It is widely used in the fields of construction machinery and heavy machinery. QD can handle the complex molding needs of cast steel materials with processes such as investment casting.
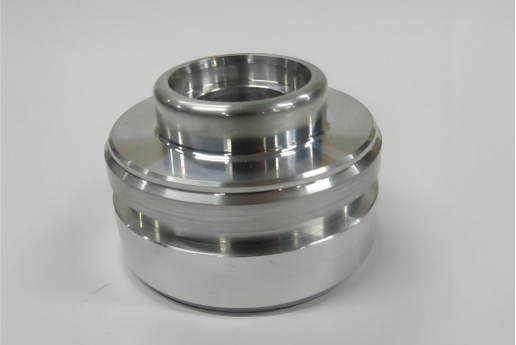
Stainless steel
Stainless steel is an alloy steel with a high chromium content. Its most notable feature is its excellent corrosion resistance. In addition:
- Good mechanical properties. Good strength and toughness.
- High surface finish. Good aesthetics. Easy to clean.
Due to its outstanding corrosion resistance. Stainless steel is often used in food processing equipment, medical equipment, chemical pipelines, marine engineering components, etc. These scenarios require extremely high corrosion resistance of the material.
QD can meet the special requirements of medical, petroleum and other industries for stainless steel castings through customized services. Whether it is small batch or large-scale production, product quality can be guaranteed.
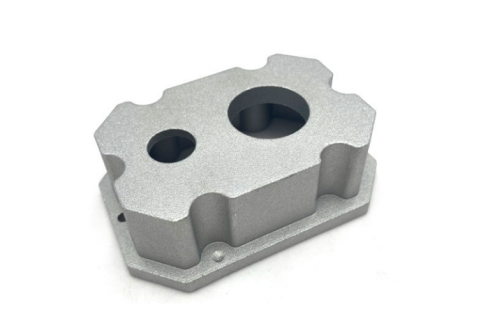
Carbon Steel
- Relatively low price. Good processing performance.
- Strength increases with carbon content. However, plasticity and toughness decrease.
Carbon steel is mainly composed of iron and carbon. According to the carbon content. It can be divided into low carbon steel, medium carbon steel and high carbon steel. Its characteristics are:
Wide range of applications. Low carbon steel can be used to make stampings and welded parts, such as automobile body parts. Medium carbon steel is suitable for making parts such as shafts and gears that require a certain strength and toughness. High carbon steel can be used to make springs, knives, etc.
QD’s various casting processes can adapt to different needs of carbon steel. Provide reliable carbon steel castings for the automotive parts, machinery and other industries.
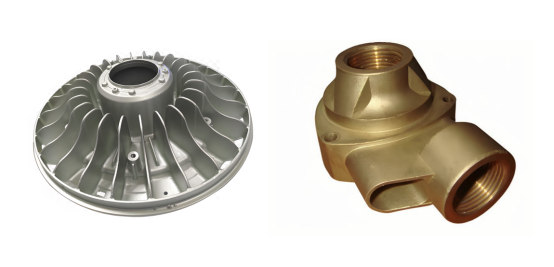
Casting non-ferrous alloys
There are many types of cast nonferrous alloys. Among them, aluminum alloys and copper alloys are the most commonly used.
Aluminum Alloy
- Low density and light weight.
- Good thermal conductivity and electrical conductivity.
- Widely used in aerospace, automobile manufacturing, electronic equipment and other fields. Such as aircraft parts, automobile engine pistons, mobile phone casings, etc.
Aluminum alloy castings produced by QD have good dimensional accuracy, surface finish and mechanical properties. Commonly used aluminum alloy grades include A356, A380, 6061, etc. They can accurately match the needs of different scenarios. They are widely used in industries such as aerospace, automobile, electronics, etc. that have high requirements for material performance.
Copper Alloy
- It can be divided into bronze and brass.
- Brass uses zinc as the main alloying element. It has good plasticity and processing properties. The price is relatively low. It is often used to make pipe fittings, decorative parts, etc.
- In addition to zinc, bronze also contains tin, lead, aluminum and other elements. It has better wear resistance, corrosion resistance and mechanical properties. It is suitable for making bearings, gears, electrical components, etc.
Copper alloys have excellent overall electrical and thermal conductivity. They are widely used in radiators, hydraulic system accessories, and other scenarios. QD can provide suitable casting solutions based on the performance requirements of copper alloys in different industries.
Factors to consider when selecting casting materials
When choosing casting materials, the following key factors should be considered comprehensively:
Mechanical properties
According to the use environment of the product. The requirements for mechanical properties. Such as material strength, toughness, hardness, and wear resistance are clearly defined. When providing services to customers. QD will first recommend suitable materials based on the mechanical properties of the product. Ensure that the castings meet the use requirements.
Corrosion resistance
If the product is used in a corrosive environment. Such as humidity, acid or alkali. Materials with strong corrosion resistance should be given priority. For orders with corrosion resistance requirements. QD will combine material properties and process characteristics. Ensure the stability of castings in complex environments.
Cost
Cost includes the price of the material itself, processing costs and subsequent maintenance costs. Under the premise of meeting performance requirements, cost-effective materials should be selected. QD supports small batch production. It can control costs while meeting customers’ needs for castings of different materials.
Casting process adaptability
Different materials have different casting properties. So they need to be selected in combination with production processes. Our masters a variety of casting processes and can match the optimal process according to material characteristics. Ensure production efficiency and product quality.
Subsequent processing requirements
Some products need to be processed by cutting, welding, heat treatment and other subsequent processing. The processing performance of the material is very important. For example, carbon steel has good welding performance and is easy to assemble. Stainless steel is difficult to cut and process, and the processing cost needs to be considered. We will fully consider the customer’s subsequent processing needs when selecting materials. Provide casting products that are easier to process.
Conclusion
The selection of casting materials requires a comprehensive consideration of performance, cost, process and other factors. Whether it is cast iron, cast steel, stainless steel, carbon steel, or non-ferrous alloys represented by aluminum alloys and copper alloys, they all require professional foundry companies to process and produce. As a foundry covering a variety of processes and serving many industries. QD can provide small-batch, customized casting solutions based on different material properties and customer needs. Helping various industries to create high-quality casting products.