Manufacturing experts are familiar with the different types and advantages and disadvantages of casting processes. The main types include sand casting, investment casting, die casting, and centrifugal casting. Each casting process has its own unique advantages and disadvantages that affect factors like speed, cost, and product quality. Understanding the types and advantages and disadvantages of casting processes helps companies produce better-performing products and select the most efficient manufacturing method.
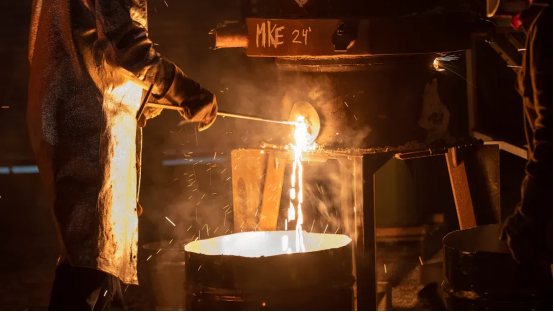
Key Points
- Casting forms metal by pouring liquid metal into molds. This helps make parts with complex shapes and details.
- Sand casting is cheap and flexible. It works well for big, heavy parts. But the surfaces are rough and not very exact.
- Investment casting makes parts that are very smooth and exact. It is good for small batches and complex shapes.
- Die casting uses metal molds to make many smooth, exact parts fast. It is best for making lots of parts at once.
- Centrifugal casting spins molds to make strong, round parts. It is good for making pipes and rings without defects.
What Is Casting?
Definition
Casting is a way to make metal parts. First, workers melt metal until it is liquid. They pour the liquid metal into a mold. The mold has the shape they want. The metal cools down and becomes hard. When it is solid, workers take off the mold. Now, the metal part is finished. Casting helps make parts with tricky shapes and small details. Factories use casting for cars, planes, and machines. It works with many metals like iron, steel, aluminum, and copper.
Importance
Casting is very important in making things today. It lets companies make parts with shapes that are hard to get in other ways. Many businesses use casting because it makes strong and complex parts for less money. Almost all durable goods have cast parts inside. This shows casting is needed for many things we use.
Sand Casting
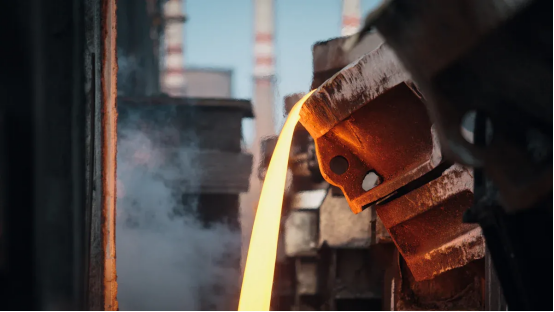
Process
Sand casting makes metal parts in several steps. First, workers mix sand with clay and water or chemicals. This makes the sand strong. Next, they press a pattern into the sand. This forms the shape of the part. The mold has two halves called cope and drag. If the part needs holes, workers make sand cores. They put the cores inside the mold. Then, workers melt metal in a furnace. The hot metal turns into liquid. They pour the liquid metal into the mold. Workers do this carefully to avoid mistakes. The metal cools down and gets hard inside the mold. After it is solid, workers break the sand mold. They take out the new metal part. Last, they clean the part and remove extra sand. They also smooth any rough edges.
QD uses new sand casting methods. This helps every step make high-quality parts.
Features
Feature | Sand Casting Characteristics | Compared to Other Methods |
Mold Material | Uses sand molds that are single-use | Die casting uses permanent metal molds |
Pattern | Wooden or metal pattern shapes the cavity | Investment casting uses wax patterns |
Material Range | Works with many metals like iron, steel, aluminum, and bronze | Some methods work with fewer metals |
Part Size | Good for large and heavy parts | Die casting fits smaller, lighter parts |
Surface Finish | Rougher surface, often needs extra machining | Die casting and investment casting are smoother |
Dimensional Accuracy | Lower accuracy, but good for many uses | Other methods can be more precise |
Advantages
- Sand casting is inexpensive. Sand molds and tooling are low cost.
- A shop can make one or more parts with this process.
- It is suitable for a variety of metals. Such as steel, iron, aluminum and bronze.
- Sand casting can create large, heavy and complex shapes.
- JC Casting provides custom sand casting services for a variety of projects.
Applications
- Automotive: Engine blocks, cylinder heads, and transmission cases
- Aerospace: Aircraft turbines, jet engine parts, and support equipment
- Energy and Power: Turbine housings and generator parts
- Construction Machinery: Excavator buckets, gearboxes, and crane components
- Heavy Industry: Pumps, valves, and large machine parts
Sand casting is flexible and does not cost much. Many companies use it to make strong, big, and complex metal parts.
Investment Casting
Process
Investment casting is also called lost wax casting. It uses many steps to make metal parts. First, workers make a wax model that looks like the final part. They put many wax models together in a tree shape. Next, they dip this tree into a ceramic liquid. Then, they cover it with tiny ceramic pieces. They do this coating step many times. The ceramic shell gets strong and hard. After it dries, workers melt out the wax. This leaves a hollow ceramic mold. They pour hot metal into the mold. The metal cools and becomes solid. Workers break the ceramic shell to get the metal parts. Last, they clean, finish, and check the parts.
Features
The investment casting process produces high-precision, smooth-surfaced parts. It uses a smooth wax pattern and a fine ceramic shell to create parts with extremely close tolerances. The process can produce thin-walled, detailed shapes. This is not possible with other casting methods. The ceramic shell has a better surface finish than sand casting. Investment casting is suitable for a wide range of metals. Such as stainless steel and high-temperature alloys. These characteristics make it ideal for manufacturing parts that require extreme precision and fineness.
QD’s investment casting process is superb. It is capable of producing parts with extremely high precision and smooth surfaces.
Advantages
Feature | Investment Casting Advantages | Compared to Sand Casting | Compared to Die Casting |
Dimensional Accuracy | Very precise and tight tolerances | Sand casting is less precise and rougher | Die casting is limited by its tools |
Surface Finish | Very smooth surfaces, less finishing needed | Sand casting is rougher | Die casting is smooth but uses fewer alloys |
Design Complexity | Can make complex shapes and thin walls | Sand casting cannot make very complex shapes | Die casting cannot make all shapes or use all alloys |
Alloy Flexibility | Works with many alloys, even superalloys | Sand casting uses many alloys but is less precise | Die casting uses softer alloys |
Production Volume & Cost | Good for small to medium batches with high quality | Sand casting is cheaper for big batches | Die casting is fast but tools cost more |
Repeatability | Makes parts the same every time | Sand casting is less consistent | Die casting is consistent but tool-limited |
Applications
- Aerospace: Used for turbine blades, engine parts, and light but strong parts.
- Automotive: Used for engine parts, gearboxes, and suspension parts that must be strong and light.
- Medical: Used for surgical tools, implants, and other small, detailed parts.
- Energy: Used for pump cases and turbine parts that work in tough places.
Investment casting helps companies make parts with tricky shapes, small details, and smooth surfaces. JC Casting gives good solutions for tough jobs in aerospace, cars, medical, and energy fields.
Die Casting
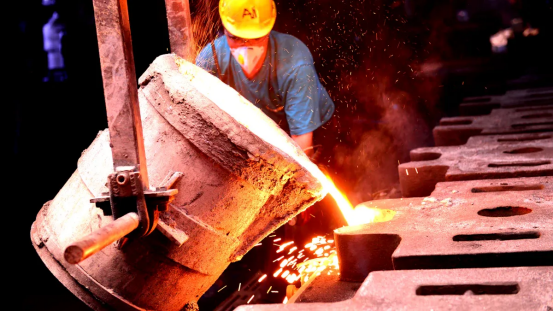
Process
Die casting uses a metal mold called a die. Workers first look at the plans and pick the right tools. They clean the die and put on special oil. This helps the metal move better. The die goes into a machine and is lined up. Workers heat the die before starting. Then, hot liquid metal is pushed in with high pressure. The metal fills the die and cools down fast. The machine opens the die when the part is ready. Pins push the new part out. Workers cut off extra bits and check if the part is good.
Die casting machines can make many parts every hour. Using machines makes the work quick and steady.
Features
- The die casting process uses high pressure to force metal into a die, producing parts with thin walls and small details.
- The process is fast. Hundreds of parts can be produced per hour.
- The dies are made of high-strength steel. They are durable.
- The finished product is compact in size. They are usually very close to the design drawings.
- Machines can help trim and finish the part. They give it a smoother appearance.
- Due to the high cost of the die, die casting is best suited for mass production.
Advantages
- The die casting process produces parts quickly. Customers do not need to wait for a long time.
- The parts look almost the same. High quality.
- The machine does most of the work. Saves costs and ensures worker safety.
- The parts are smooth. Almost no additional processing is required.
- The method can produce parts with complex shapes and thin walls. Saves metal.
- The high pressure prevents air from entering. Makes the parts stronger and more durable.
Advantage | Description |
Speed | Makes many parts quickly for big orders |
Accuracy | Parts are the right size and shape |
Consistency | All parts look and work the same |
Cost Efficiency | Cheaper per part when making a lot |
Applications
- Automotive: Used for engine blocks, gear cases, and car parts.
- Electronics: Used for heat sinks, covers, and plugs.
- Consumer goods: Used for appliance parts and sports gear.
- Machinery: Used for cylinders, gears, and covers.
- Aerospace: Used for plane frames and engine covers.
Die casting works with metals like aluminum, zinc, magnesium, and copper. Many companies use die casting because it is fast, accurate, and makes strong parts with lots of detail.
Centrifugal Casting
Process
Centrifugal casting uses a spinning mold to shape metal. Workers coat the mold so metal will not stick. They pour hot metal into the spinning mold. The mold spins very fast, between 500 and 1500 times each minute. The spinning pushes the metal to the mold’s sides. The metal cools and gets hard from the outside first. Spinning moves lighter stuff and dirt to the middle. When the metal is solid, workers take out the part. They often cut or clean the inside to remove extra material. Controlling the speed, heat, and cooling helps make strong parts. This also stops air bubbles and holes from forming.
Features
Centrifugal casting is special because it uses spinning force. This force makes the metal better and stronger. Heavy metal moves to the outside, making the walls tough. The metal gets hard from the outside to the inside. This stops holes in the middle and makes the grain even. The process can make parts up to 30% stronger than gravity casting. Using a vacuum or other ways can stop gas bubbles and keep metal clean. Factories can pick the wall thickness and how the grains flow. This helps make parts with the right size and shape. Centrifugal casting works best for round, hollow parts like pipes and rings.
Centrifugal casting makes parts with fine grains and few problems. These parts are good for hard jobs.
Advantages
- Makes round parts with even walls and smooth outsides.
- The grain is better, so parts are strong and bend well.
- Fewer air pockets and dirt, so parts are solid.
- Parts are made fast and cost less, good for tubes and rings.
- No need for a core when making hollow parts.
- Easy to change wall thickness and shape.
- Can make parts with layers to stop rust.
Advantage | Description |
Uniformity | Walls and shapes are even |
Strength | Parts are strong and hard to break |
Defect Reduction | Fewer holes and dirt inside |
Cost Efficiency | Fast to make, less extra work needed |
Versatility | Works for many metals and sizes |
Applications
- Centrifugal casting is used to make many important parts.
- Pipes and tubes for water, oil, and gas
- Engine cylinders and sleeves for cars and trucks
- Rings, bearings, and bushings for machines
- Hydraulic and marine parts
- Pipes for fire safety systems
- Special shapes like cones, valves, and liners
Factories use sideways molds for long pipes and tubes. Up-and-down molds are best for rings and short parts. This process makes strong, solid, and rust-proof parts that last a long time. Many businesses use centrifugal casting for good, strong parts.
Knowing about the types and advantages and disadvantages of casting processes helps people pick the best way for each job. Every process has things it does well and things it does not do well. There are other ways too, like permanent mold, continuous, lost foam, and plaster casting, etc. These ways are good for special jobs. such as making very smooth parts or using special metals.
Comparison Table
The table below shows how the four main casting processes are different. It tells how each process works, how much it costs, and how good the finished part is.
Casting Method | Process Description | Cost Considerations | Product Quality Characteristics | Typical Applications |
Sand Casting | Sand mold, molten metal poured in | Low initial cost, good for small runs | Less precise, rougher surface, large parts | Engine blocks, machinery |
Investment Casting | Wax pattern, ceramic shell, metal poured | Higher cost, multi-step, not for high volume | High precision, smooth finish, complex shapes | Aerospace, medical devices |
Die Casting | Metal injected under high pressure into steel die | High mold cost, best for large volumes | High accuracy, smooth surface, tight tolerances | Automotive, electronics |
Centrifugal Casting | Metal poured into spinning mold | Moderate cost, efficient for cylinders | Dense, strong parts, fewer defects, limited inner size | Pipes, tubes, rings |
Note: The types and advantages and disadvantages of casting processes change based on what the job needs, like how big, what shape, and how many parts.
Selection Criteria
When picking a casting process, people should think about some key things:
- Production volume: Sand casting and investment casting are good for small numbers. Die casting is better for making lots of parts.
- Precision and surface finish: Investment casting and die casting make the most exact and smooth parts.
- Cost: Sand casting is cheapest to start. Die casting costs more at first but is cheaper if you make many parts.
- Part shape and size: Centrifugal casting makes strong, round parts. Sand casting can make big and tricky shapes.
- Material: Some ways work better with certain metals. For example, die casting uses aluminum, zinc, or magnesium.
- Quality needs: Each way has different chances for mistakes. Quality checks look for things like holes or cracks.
People should match the types and advantages and disadvantages of casting processes to what their project needs. This helps them get the best mix of quality, speed, and price.
Knowing about the types and advantages and disadvantages of casting processes helps companies pick the best way. Choosing the right process makes products better, saves money, and helps things work well.
Casting Method | Advantages | Disadvantages |
Sand Casting | Saves money and works for big parts | Not as exact, surface is rough |
Vacuum Die Casting | No air holes, can make thin pieces | Costs a lot, setup is hard |
Gravity Die Casting | Makes strong parts with better size | Molds are pricey, cracks can happen |
Casting experts like QD have independent factories and advanced production equipment. Workers are proficient in a variety of casting processes. They can effectively help companies avoid problems and escort customers’ projects.