Stainless steel casting
Stainless steel is an iron-based alloy containing alloying elements such as chromium. It prevents oxygen from diffusing to the steel surface to prevent further surface corrosion. It has good strength, toughness and processability. It is one of the most commonly used materials in casting production. Stainless steel casting is a metal processing process that produces custom stainless steel parts. In castings, stainless steel is commonly used in a variety of industries. Including hydroelectric power, locomotives, pumps, valves, power generation, automobiles, aviation and many different types of industrial processing equipment. JC Casting produces almost all grades of stainless steel castings.
Characteristics and advantages of stainless steel casting
Stainless steel castings have the following characteristics:
- Strong corrosion resistance: Chromium elements form a passivation film. Resistant to acid, alkali, salt spray and oxidation corrosion. Suitable for harsh environments such as humidity and chemical industry.
- Excellent mechanical properties: Wear resistance. High temperature resistance. Stable strength at high temperature. Good fatigue resistance.
- Hygiene and safety: Smooth surface and easy to clean. Non-toxic. Suitable for food and medical fields.
- Flexible molding: Complex structural parts (such as special-shaped pipes and valve bodies) can be made through casting process. Adapt to high-precision component requirements.
Stainless steel castings have several advantages. The main advantages include:
1. Wide material adaptability: The alloy composition can be adjusted according to needs (such as adding nickel and molybdenum). Optimize corrosion resistance, strength and other properties.
2. Corrosion resistance: The chromium content in stainless steel forms a corrosion-resistant protective layer. To ensure a longer service life of the casting.
3. Versatility: Stainless steel castings are available in a variety of grades and surface treatments. They can be customized to meet the specific requirements of different environments and applications.
4. High cost-effectiveness: Compared with other materials. Stainless steel may have a higher upfront cost. But it has a long service life and low maintenance requirements. Cost savings are usually achieved over time. And batch casting can reduce the processing cost of complex parts. Reduce cutting losses.
5. Hygiene: Stainless steel is easy to clean and maintain. It is very suitable for food and pharmaceutical industry applications where hygiene is critical.
6. Diverse application scenarios: Covering construction (decorative components). Energy (oil pipelines). Chemical (reactors). Automobile (engine parts) and other fields. Meet the needs of diverse working conditions.
Common stainless steel material classification
304 | General purpose stainless steel. Good corrosion resistance. Suitable for food equipment and building decoration. |
316 | Adding molybdenum element makes it more resistant to corrosion. Especially to seawater and chemical media. |
2205 | Austenite + ferrite dual phase structure. High strength and stress corrosion resistance. |
17-4PH | Precipitation hardening by heat treatment. Combines high strength and corrosion resistance. |
420 | High carbon content. Excellent hardness and wear resistance. Suitable for wear-resistant parts (such as bearings). |
430 | Good corrosion resistance and formability. Low cost. |
Applications of Stainless Steel Casting
Since stainless steel has ideal qualities such as corrosion resistance and high strength. It is widely used in various industries. Some common applications of stainless steel include:
- Automotive Industry
Parts exposed to harsh environments and high stresses. There are extensive and critical applications in the automotive industry. Including exhaust system components, turbocharger components, suspension components and brake system components.
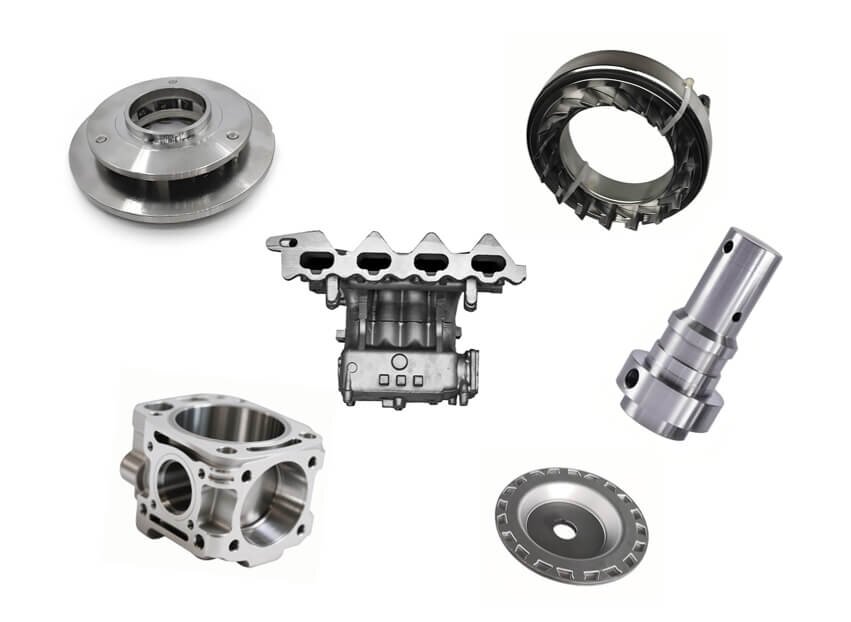
- Construction Industry
Stainless steel castings are widely used in various building structures, decorations and functional parts. Such as bridge and steel structure connectors, decoration and appearance parts, functional facilities and infrastructure, etc.
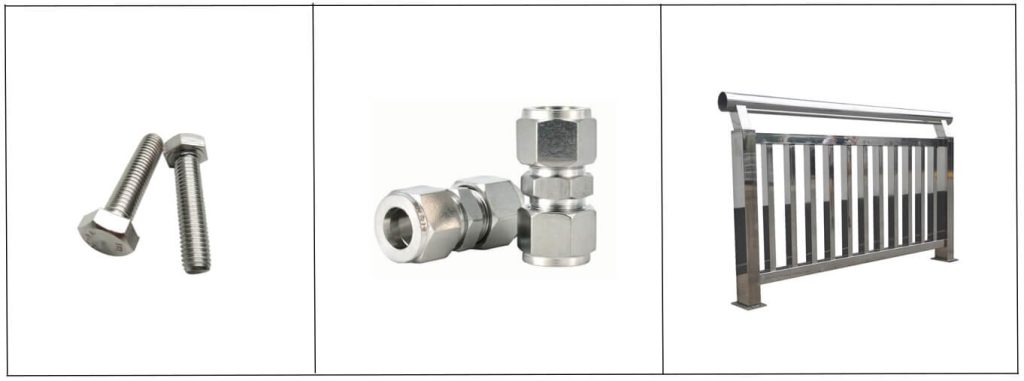
- Hydropower
With excellent anti-scouring, corrosion resistance, and high-pressure resistance, stainless steel castings play a key role in the field of hydropower. They are widely used in turbine units, water delivery systems, and supporting facilities. Such as core components of turbine generator units, water delivery and flow system components, water pumps, and water treatment equipment.
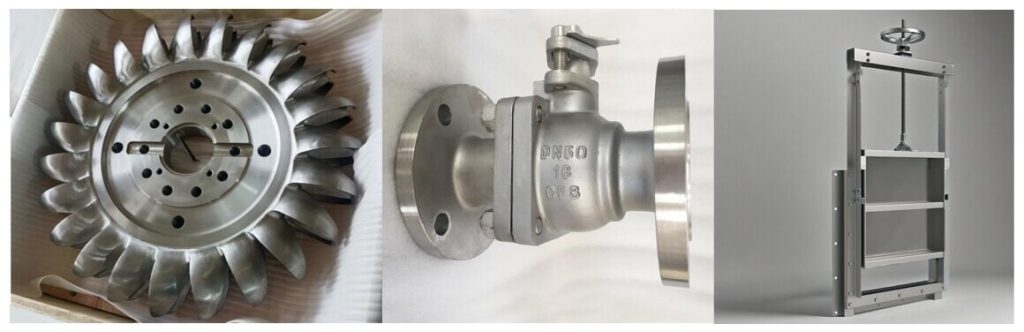
- Food Processing Industry
Stainless steel is suitable for food processing and storage. It has excellent strength and easy-to-clean characteristics. Its corrosion resistance is particularly suitable for handling highly acidic foods such as lemons. It is widely used in equipment, pipelines and structural parts that come into direct contact with food. Such as food processing molds, baking and cooking equipment parts, etc.
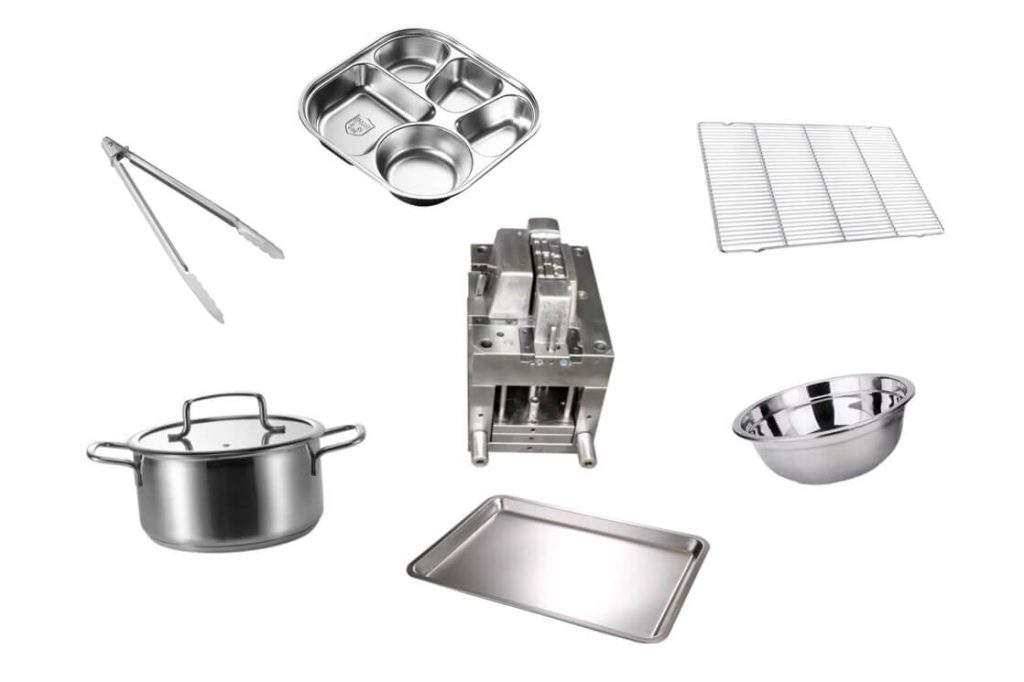
- Medical and pharmaceutical applications
Stainless steel is widely used in medical devices and pharmaceutical equipment that come into contact with the human body because it is easy to sterilize.
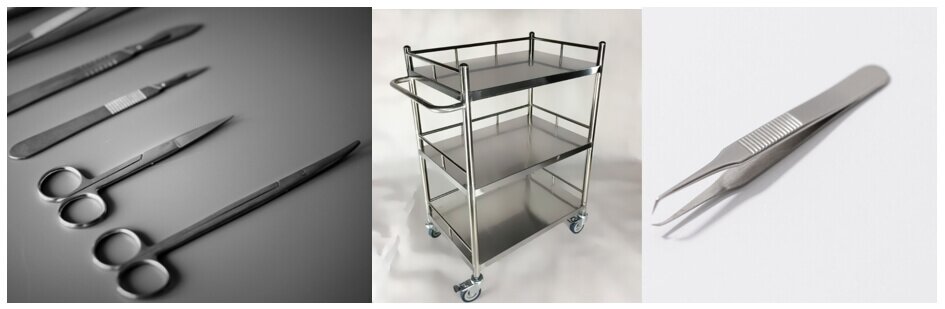
Stainless Steel Casting Process
At JC Casting, we are equipped with the most advanced casting equipment and multiple production lines to ensure the accuracy and consistency of each casting we produce. We usually use sand casting and investment casting to produce stainless steel castings.
Sand Casting
Process Features: Using molding sand as the molding material. Low cost. Strong adaptability. Suitable for medium and large parts and complex structure castings.
1. Modeling preparation: Make a wooden or metal mold according to the casting design. Prepare the molding sand (quartz sand + binder).
2. Molding:
- Divided into upper mold and lower mold. Put the pattern into the sand box. Fill the molding sand tightly. After taking out the pattern, a casting cavity is formed.
- Open the pouring system (gate, riser). Used for metal liquid inflow and shrinkage compensation.
3. Closing: Align the upper mold and the lower mold and close them. Fix the position to prevent misalignment during pouring.
4. Melting and pouring: Stainless steel is melted in an electric arc furnace or induction furnace. When the temperature reaches about 1500℃, it is poured into the sand mold.
5. Cooling and cleaning: After the castings have cooled, unpack and remove the sand. Remove the sand mold. Cut the pouring and riser. Perform shot blasting, machining and flaw detection.
Investment Casting (Lost Wax Casting)
Process features: wax model is used as the pattern. It is formed through shell making, dewaxing, pouring and other processes. It is suitable for complex precision castings.
- Making wax models: Use wax material to make wax models that match the shape of the casting. Small wax models can be mass-produced by pressing and then combined into wax model sets.
- Shell making: Dip the wax mold into a slurry of refractory materials (such as silica sol, water glass) and sand. Repeatedly apply multiple layers to form a hard shell (usually 5-10 layers).
- Dewaxing: Heat the shell (about 80-120℃) to melt the wax pattern and flow out. Leaving a hollow shell.
- Firing and pouring: The shell is calcined at high temperature (about 900-1200℃) to remove impurities. At the same time, the stainless steel is melted and poured into the shell while it is hot.
- Sand removal and cleaning: After cooling, break the shell. Take out the casting. Clean the burrs and pouring risers. Perform heat treatment and surface treatment.
JC Casting is specialized in stainless steel sand casting and investment casting processes. We can design and customize each cast stainless steel part to meet your needs.
Value-added Services—Surface Treatment Options of JC Casting
Process | Method | Introduction | |
Mechanical surface treatment | Frosting | Use sandpaper, grinding wheel or wire drawing machine to form parallel lines on the surface | |
Polishing | Mechanical polishing | Polishing with cloth wheel + polishing paste. Mirror effect. Suitable for tableware and accessories. | |
Electrolytic polishing | Using electrochemical principles to dissolve microscopic protrusions on the surface. It has a higher flatness and can enhance corrosion resistance. It is often used in medical devices. | ||
Sandblasting | High-pressure blasting of sand particles hits the surface. Creates a matte, rough surface. Can be used as a primer for subsequent coatings. | ||
Chemical surface treatment | Pickling | Use nitric acid + hydrofluoric acid solution to remove the surface oxide scale. Reveal the metallic luster. At the same time, a passivation film is formed. | |
Passivation | Immerse in passivation solution. Promote the formation of dense Cr₂O₃ on the surface. Improve corrosion resistance. | ||
Electrochemical surface treatment | Electroplating | Plate a metal layer (such as nickel, chromium) on the surface to enhance wear resistance or aesthetics. | |
Surface coating treatment | Painting | Spraying organic coatings. Forming a colored protective layer. Used for corrosion protection of outdoor facilities (such as guardrails). | |
PVD | Through vacuum sputtering, metal ions such as titanium and zirconium are deposited into films. Commonly used in knives and watch straps. |
Collaboration with JC Casting
At JC Casting, we are proud to be an ITAR and ISO certified factory. We have our own independent foundry and advanced processing equipment. We specialize in providing high-quality stainless steel castings for a wide range of industries. With more than 20 years of casting experience. We can guarantee you that we will provide the fastest delivery time in the industry on the basis of providing the highest quality stainless steel parts. Ensure that your project goes as planned.
As a professional stainless steel casting manufacturer and supplier. Quality is at the core of everything JC Casting does. Our quality assurance program includes:
- Raw material testing: We perform strict performance tests on all raw materials to ensure that they meet the specifications.
- Production process control: Closely monitor the production process at all stages throughout the process to ensure the consistency and accuracy of the process.
- Finished product final inspection: Each casting is fully inspected, covering verification of dimensional accuracy, surface finish and other dimensions.
If you are looking for a reliable partner for your stainless steel casting needs. JC Casting is here to help. For more information about stainless steel. Or to request a quote for a custom project. Please contact the JC team.
FAQ
1. What is investment cast stainless steel?
Investment casting stainless steel is a type of stainless steel produced using the investment casting process. This process can produce stainless steel castings with complex shapes, high dimensional accuracy and good surface quality.
2. Which stainless steel is best?
There is no absolute “best” stainless steel. Different types of stainless steel are suitable for different scenarios due to their composition and performance. For example, 304 stainless steel has good corrosion resistance and is often used in food, medical and other fields. 440 stainless steel has high hardness and is suitable for making tools such as knives. Which stainless steel to choose depends on the specific usage requirements and working conditions.
3. What are the benefits of investment casting?
Investment casting has many benefits. It can produce castings with complex shapes, high dimensional accuracy and good surface finish. No or only a small amount of machining is required. A variety of alloy materials can be cast, including stainless steel, alloy steel, etc. It can also achieve mass production. And the production cycle is relatively short. It helps to reduce production costs.
4. Is cast stainless steel strong?
Cast stainless steel has high strength. Through reasonable composition design and heat treatment process, cast stainless steel can obtain good mechanical properties, which can meet the use requirements of different engineering structures and mechanical parts.
5. Does cast stainless steel rust?
Cast stainless steel has good corrosion resistance under normal use environment, but it is not absolutely rust-free. When it comes into contact with specific corrosive media, such as high-concentration acid and alkali solutions, or under harsh environmental conditions, as well as improper maintenance, scratches or damage on the surface, cast stainless steel may also rust.