Valves are key control components for regulation, diversion and shutoff in industrial pipeline systems. As a foundry focusing on high-reliability valve castings. QD focuses on material adaptation, process innovation and defect prevention and control. It provides customized solutions for different fields.
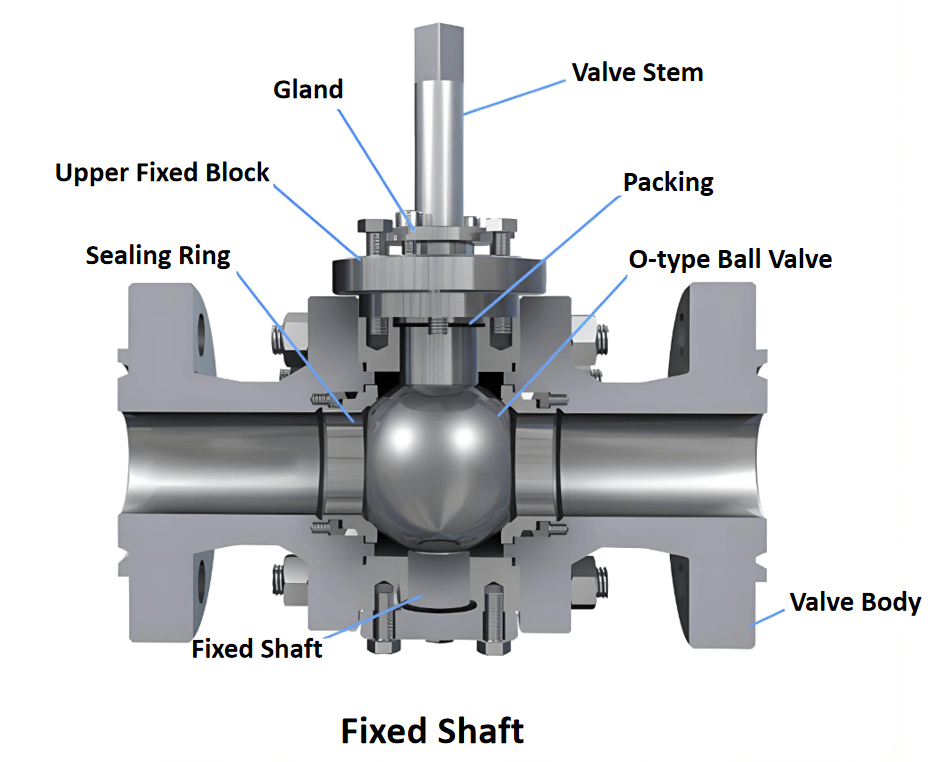
Common valve types
Selecting the appropriate valve type is the first step to ensure efficient operation of the system.
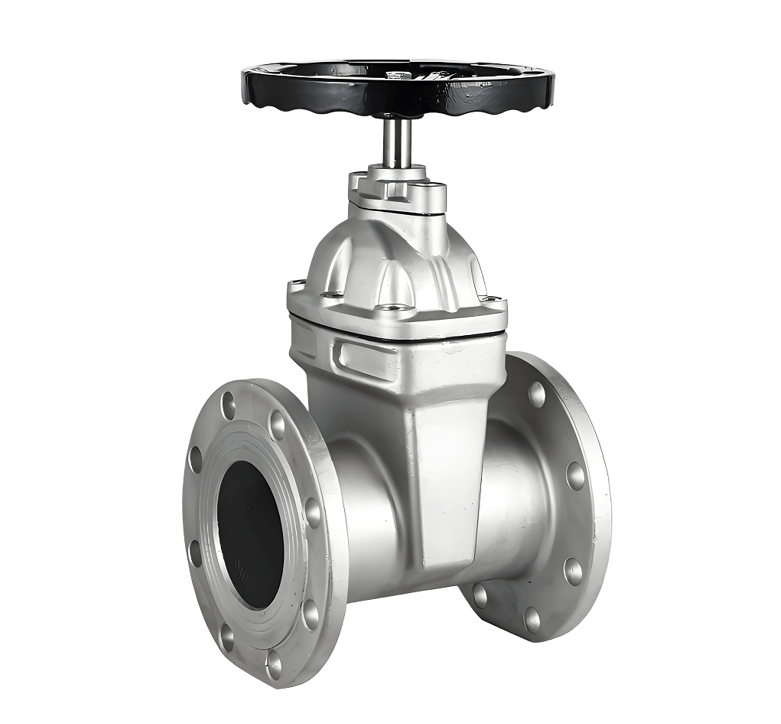
1. Gate valve
- Core function: Full opening and closing as the core function. The vertical lifting of the gate plate realizes the complete opening and closing or full-diameter flow of the medium in the pipeline.
- Application scenarios: Oil trunk pipelines, large storage tank imports and exports
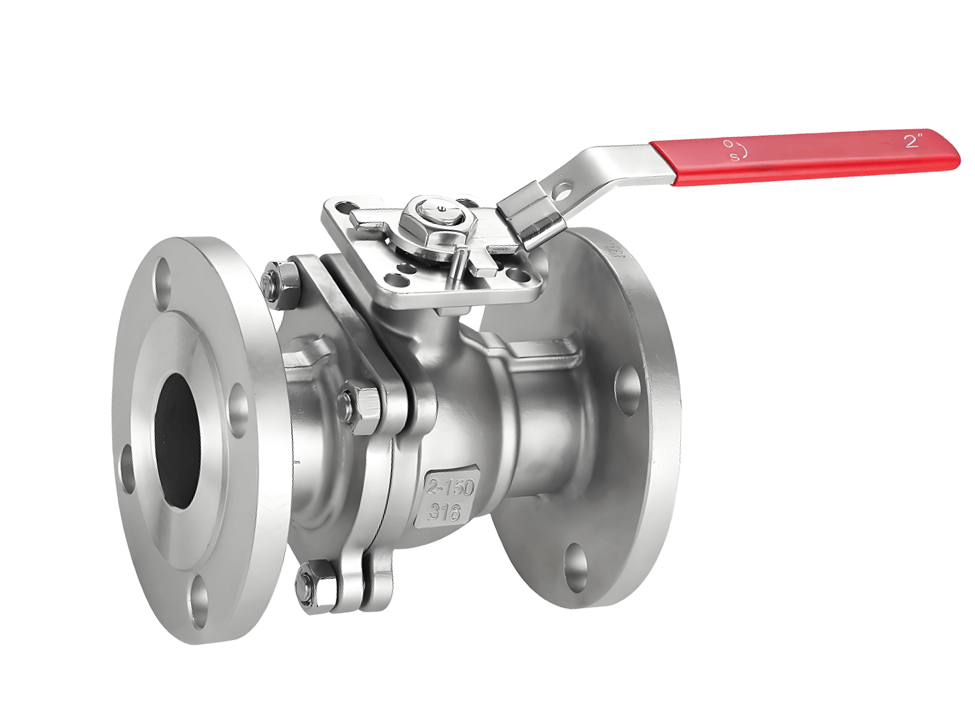
Ball valve
- Core function: 90° rotation to quickly cut off the fluid. It has the advantages of rapid opening and closing, small flow resistance, and excellent sealing performance.
- Application scenarios: Chemical safety system, LNG storage and transportation equipment
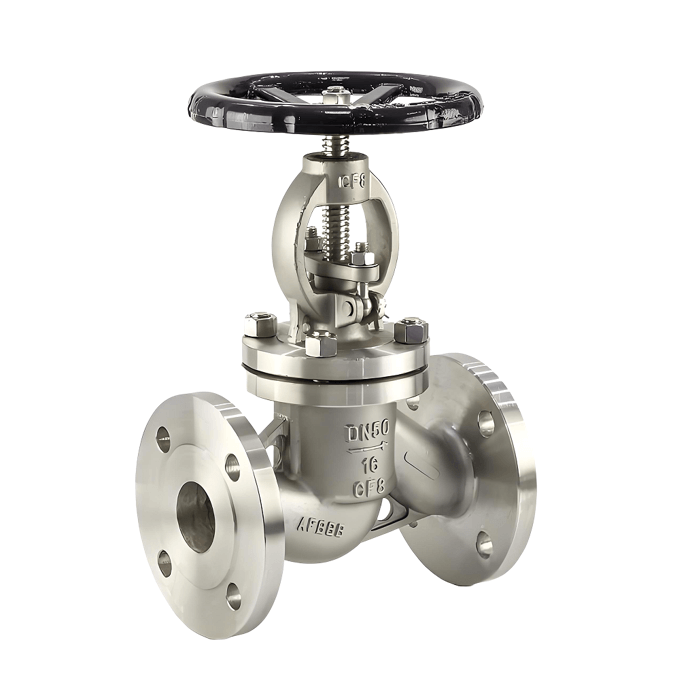
Globe Valve
- Core function: Accurately adjust the flow rate through the linear movement of the valve disc. The medium flow rate can be accurately controlled within the range of 0-100%.
- Application scenarios: Power plant steam system, fine chemical process
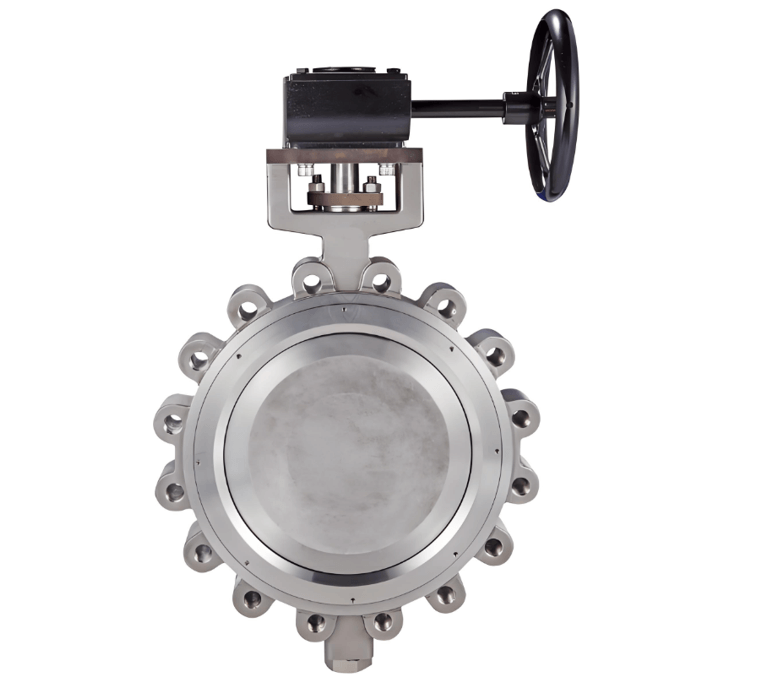
Butterfly valve
Core function: Disc-type opening and closing parts. Suitable for flow control of large-diameter pipes.
Application scenarios: Municipal water supply network, HVAC system
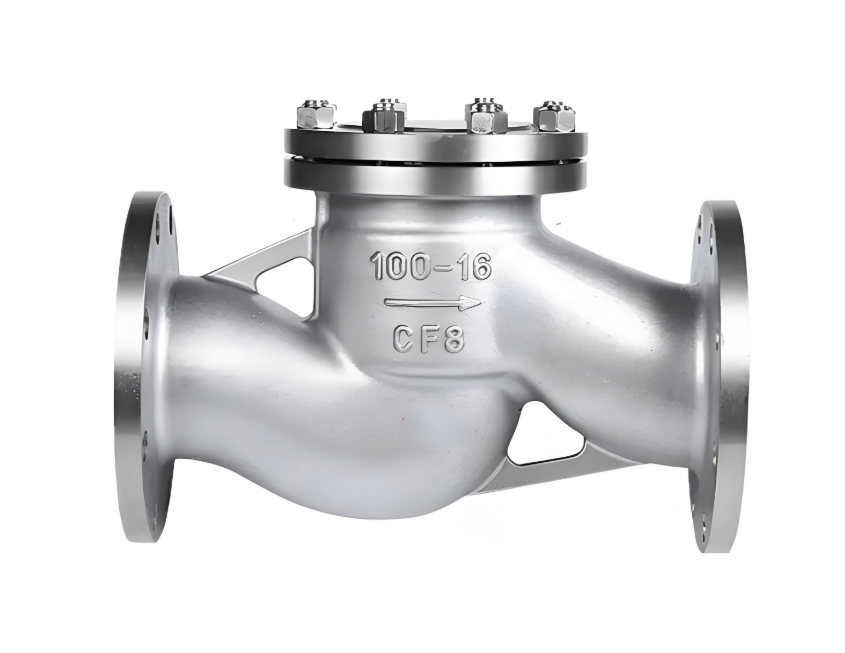
Check valve
Core function: Automatic opening and closing by relying on the pressure difference of the medium itself. The core function is to prevent the medium from flowing back. Protect the safety of the pump station
Application scenario: Water pump outlet, compressor pipeline
Three core casting materials
Material | Core Advantages | QD Casting Process |
Brass | Antibacterial, economical, easy to process | Sand Casting |
Stainless steel | Corrosion resistance, high temperature resistance, high strength | Investment Casting |
Ductile Iron | High strength, impact resistance, low cost | Sand Casting |
According to the medium characteristics, pressure level and use environment. QD matches the best material and process combination for customers:
Brass material is favored in drinking water treatment systems due to its natural antibacterial properties. QD sand casting process further reduces the cost of mass production, making the cost-effectiveness more prominent;
Stainless steel, as a general corrosion-resistant material, meets the hygiene requirements of food-grade pipes. The high precision of QD investment casting ensures the molding quality of complex structures;
The high strength and vibration resistance of ductile iron are suitable for high-frequency opening and closing scenarios such as municipal pipelines. The QD sand casting process gives it more stable mechanical properties.
QD casting defect prevention and control
Common defects in traditional casting, such as pores and shrinkage, can easily lead to failure of valve sealing surface and cause leakage. QD solves traditional risks from the root through three core process innovations and creates real value for customers:
Traditional risks | QD Solutions | Customer Value |
Pore Leakage | Vacuum casting process | No system downtime losses |
Insufficient shrinkage pressure | Intelligent feeding system | Extend replacement intervals by 2 times + |
Inclusion wear | Melting purity control | Reduce maintenance costs by 50% |
- Porosity is the main cause of valve leakage. The risk is higher in high-pressure environments. QD vacuum casting process avoids gas entrapment from the root. Successfully solved the high-pressure leakage problem of special valves on deep-sea oil production platforms.
- Shrinkage will reduce the pressure bearing capacity of castings and shorten the replacement cycle. QD intelligent shrinkage compensation system greatly improves the structural density through real-time monitoring and precise control. Significantly reduce costs.
- Inclusions will accelerate the wear of the sealing surface and increase the maintenance frequency. QD reduces the inclusion content to less than 1/3 of the industry standard. The maintenance cycle of ball valves in chemical companies is doubled. Annual maintenance costs are reduced by 50%.
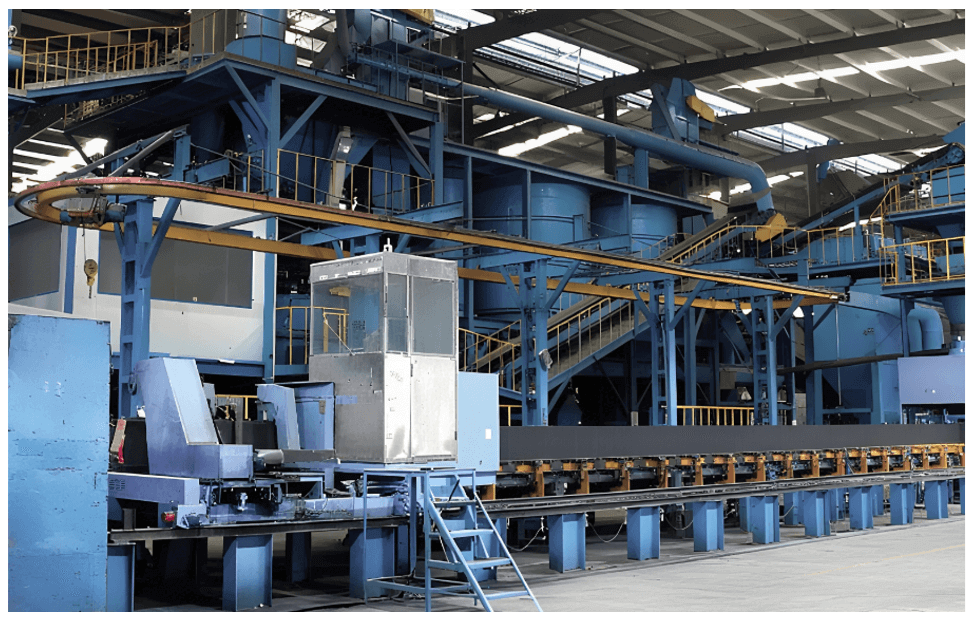
Choose QD: Full chain guarantee from demand to solution
Whether it is a butterfly valve for municipal water supply or a ball valve for deep-sea oil production. The reliability of valve castings is always the cornerstone of system safety. QD focuses on precise material matching, process innovation and defect prevention and control. Through customized processes such as sand casting and investment casting, the whole process from design to production can be controlled.
In the 20 years of serving the fields of energy, chemical industry, water affairs, etc., QD has delivered more than one million valve castings. We know that continuously reducing the cost of customer failures is the best sincerity for cooperation.
If you are troubled by the selection, material matching or reliability of valve castings, you may wish to contact us: From demand analysis to sample testing. QD will provide you with customized solutions. After all, in the field of fluid control, reliable valve castings are the starting point of all efficient operations.